MATERIAL SYNTHESIS
Material synthesis facilities consist of PLD, CVD lab and Nanoparticles lab where a wide range of facilities for sample preparation and treatment is available.
Providing state-of-the-art facilities and support for material synthesis and thin film deposition.
Thin Film Deposition Facilities
The PLD lab is equipped with variety of automated PLD chambers. This PLD system is specially used to deposit materials with high vapor pressure (volatile). The inside of the vacuum chamber is very accessible and can be cleaned to prevent any unintentional contamination from these volatile compounds. The software provides for automated sequential deposition using an intuitive program. In addition to oxides grown in other PLD system, this is commonly used to fabricate volatile oxides such as Bi based compounds (BiVO4, BiFeO3), Vanadium based compounds (VO2), Ruthenium Oxide and many others.
Sample Preparation & Treatment
The following functionalities allows fabrication of almost any compound (generally oxides) with unprecedented control, quality and small turnaround time. The patented beam scanning and target raster algorithm increases the appeal of this PLD system. Combinatorial spreads can be made in this system by carefully mixing different materials through an intuitive program. The use of RHEED allows us to tweak and understand thin film growth modes. Epitaxial, single crystalline, ultra-smooth thin films can be made due to the high temperature capabilities on lattice matched substrates. Common thin films fabricated in this system includes Perovskite Oxides, Superconducting Curates, Magnetic Oxides (Thulium Iron Garnet, Iron Oxide), Ferroelectric Oxides (BaTiO3).
The following facilities for sample preparation and treatment are available:
- The variety of furnaces for sintering PLD target pellets, as well as preparing atomic flat terraced surface of single crystal substrates for subsequent film growth processes.
- The buffered hydrofluoric acid (BHF) for achieving single-terminated perovskite substrate, by selectively etching away the surface composition such as SrO.
- Combining hydrochloric acid (HCl) and potassium iodide (KI), we have effective reducing agents that is capable of chemically etch special materials such as manganites in order to define lithographic patterns.
- Ion Beam Milling that serves as physical etching to define micro- or nano-structures.
- Separate Fumehoods for BHF, common mineral acids and organic solvents are also provided for researchers to handle volatile/fuming liquids safely.
How to Access Facilities
To access the facility, the following steps must be followed:
Contact Ngee Hong Teo (mtnh@nus.edu.sg) and Tiho (tiho@nus.edu.sg) to schedule a project meeting.
Register your personal and project details with PPMS (https://ppms.asia/nus-cde/login/)
Schedule a training or service session with our staff.
Service & Booking Fees
Booking fees will differ for NUS and Non-NUS members. More details will be published soon.
Our Partners
Find out more about our partners in Singapore:
Electron Microscopy Facility (EMF)
NUS Center for Bioimaging Sciences (CBIS)
NUS YLL School of Medicine Electron Microscopy Unit (EMU)
NTU Facility for Analysis, Characterization, Testing and Simulation (FACTS)
A*STAR IMRE Advanced Characterization and Instrumentation (ACI) Department
Contact Us
Research Fellow : Tiho@nus.edu.sg
Lab Technologist : Mtnh@nus.edu.sg
Communications : Samuel@nus.edu.sg
T11 Shared Facilities
Level 11
T-Lab Building
5A Engineering Drive 1
College of Design and Engineering
Singapore 117411
FACILITIES
Click on the icon/tab to learn more about our facilities at NUS T11:
Material synthesis
Structural Characterisation
Properties
Devices
Material Synthesis Facilities
Physical Deposition
Discover more, Click here.
The following is available at our facility: 4 Inch Chamber, 2 Inch Chamber, Big Chamber, Create Chamber, Magnetic Chamber, Small Chamber and E-beam/Thermal Evaporator.
Chemical Deposition
Discover more, Click here.
The following is available and consist of 4" CVD, 2" CVD and Graphene CVD.
Chemical Synthesis
Discover more, Click here
The facility has the equipments of Flammable and acid fume hoods, HF workstation, STF-16/180 Carbolite TF and HST-12/600 Carbolite Split TF.
Physical Deposition
Kindly note that these equipments within the section of physical deposition are only available for collaboration, except for the E-beam.
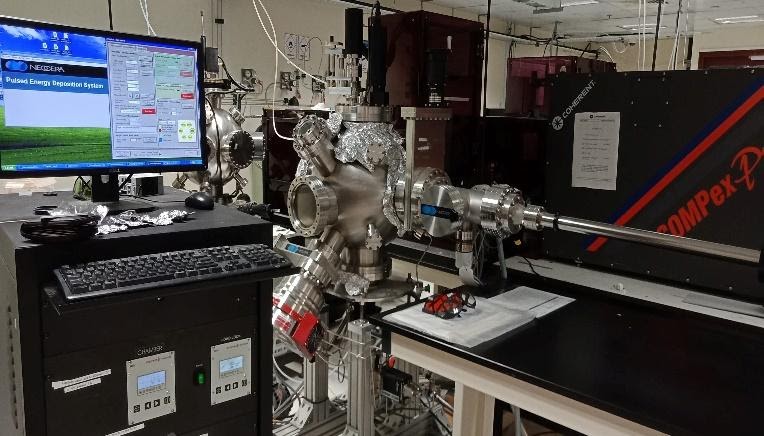
Pulsed Laser Deposition: Big Chamber
It is a convenient, automated pulsed laser deposition (PLD) system equipped with a loadlock transfer arm. It is currently used for studying oxide magnetic Skyrmion systems. The Big Chamber was manufactured by Neocera.
Technical Specifications:
Chamber size | ~50cm diameter sphere |
Target holders | 6 units of interchangeable carousels 1 inch diameter stage Adjustable height Computerized raster (~15o/s) and rotation (~40o/s) Fixed target shutter |
Substrate holder | 2 inch diameter wafer size Computerized rotation (~50o/s) Manual substrate shutter |
Substrate heater &
Temperature controller |
Resistive heating with computerized PID controller Max. heater temperature 950 oC |
Vacuum | Rotary vane pump: down to 1x10-2 Torr Pfeiffer turbomolecular pump: down to 6x10-8 Torr |
Loadlock transfer arm | Rotary vane pump: down to 1x10-1 Torr Pfeiffer turbomolecular pump: down to 1x10-7 Torr |
Gas control | Manual mass-flow-control (MFC) and manual vent Oxygen, nitrogen and argon gases are available |
Laser | Coherent Compex Pro 110 KrF excimer laser (shared):
|
Optics | Mirrors (Purchased from Thorlabs Inc.)
Focus lens (Purchased from Thorlabs Inc.):
Detachable quartz window, Transmission ~94% |
Laser energy density | Optimal spot size: 1mm x 2.5mm rectangle Achievable energy density: ~10 J/cm2 Commonly-used energy density: 1-3 J/cm2 |
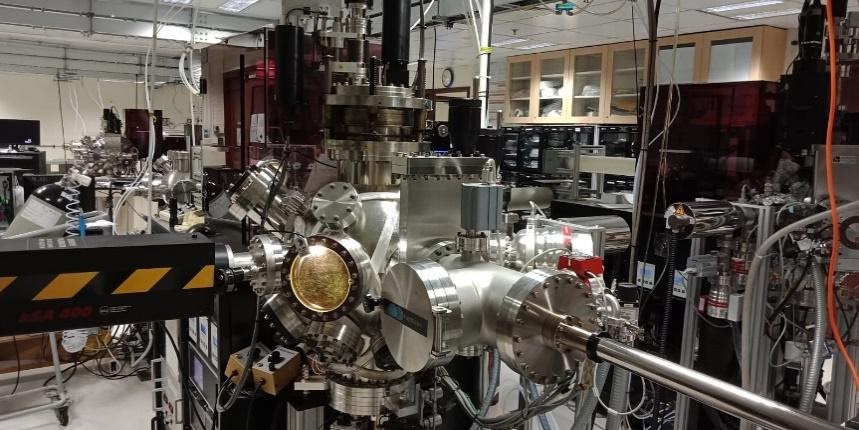
Pulsed Laser Deposition: 4 inch Chamber
Pulsed Laser Deposition (PLD) system allows deposition of materials to produce high quality oxide heterostructures and thin films. The system includes 4 inch substrate plate connected with transfer load lock chamber to load the target and substrate holder. It is also possible to monitor and control the growth rate during the deposition using the integrated Reflection High Energy Electron Diffraction (RHEED) system.
Technical Specifications
- Base pressure: 1E-8 Torr;
- Maximum heater temperature: 950oC
- Heating and cooling rate: above 900oC rate should not go above 10oC/min
- Substrate up to handle 4 inch wafer
- RHEED Chamber (Base pressure: 1E-8 Torr)
- 4inch combinatorial gradients can also be created via software routine program
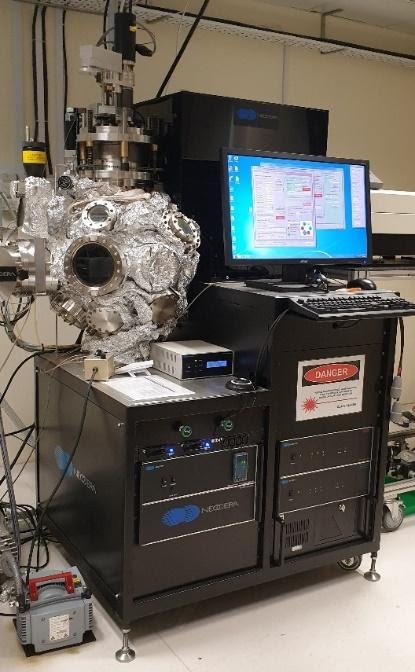
Pulsed Laser Deposition: Create Chamber
The Create Chamber was manufactured by Neocera. It is a convenient, automated pulsed laser deposition (PLD) system equipped with a loadlock transfer arm. It is currently used for studying Boron doped copper systems.
Technical Specifications
Chamber size | ~50cm diameter sphere |
Target holders | 6 units of interchangeable carousels6 inch diameter stage Adjustable height Computerized raster (~15o/s) and rotation (~40o/s) Fixed target shutter |
Substrate holder | 2 inch diameter wafer size Computerized rotation (~50o/s) Manual substrate shutter |
Substrate heater &Temperature controller | Resistive heating with computerized PID controllerMax. heater temperature 950 oC |
Vacuum | Rotary vane pump: down to 1x10-2 TorrPfeiffer turbomolecular pump: down to 6x10-8 Torr |
Loadlock transfer arm | Rotary vane pump: down to 1x10-1 TorrPfeiffer turbomolecular pump: down to 1x10-7 Torr |
Gas control | Manual mass-flow-control (MFC) and manual ventOxygen, nitrogen and argon gases are available |
Computer | Windows XP, 32-bit operating system with Neocera PLD softwareLooping routine editor for automated growth of superlattice or intermixing between >2 materials |
Laser | Solid state and Quantronix laser: Nd:YAG laser
|
Optics | Mirrors (Purchased from Thorlabs Inc.)
Focus lens (Purchased from Thorlabs Inc.):
|
Laser energy density | Optimal spot size: 1mm x 2.5mm rectangle Achievable energy density: ~10 J/cm2 Commonly-used energy density: 1-3 J/cm2 |
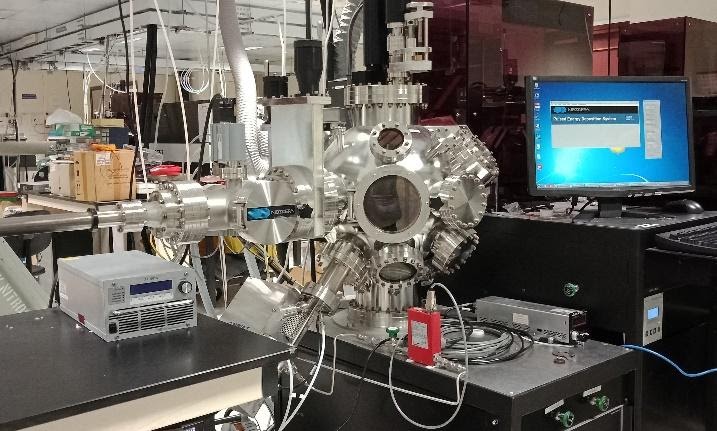
Pulsed Laser Deposition: Magnetic Chamber
It is a convenient, highly automated pulsed laser deposition (PLD) system equipped with a loadlock transfer arm. It is currently used for developing BiFeO3-based multiferroic memory devices. The Magnetic Chamber was manufactured by Neocera.
Technical Specifications
Chamber size | ~50cm diameter sphere |
Target holders | 6 units of interchangeable carousels6 inch diameter stage Adjustable height Computerized raster (~15o/s) and rotation (~40o/s) Fixed target shutter |
Substrate holder | 2 inch diameter wafer sizeComputerized rotation (~50o/s) Manual substrate shutter |
Substrate heater &Temperature controller | Resistive heating with computerized PID controllerMax. heater temperature 950 oC |
Vacuum | Rotary vane pump: down to 1x10-2 TorrPfeiffer turbomolecular pump: down to 6x10-8 Torr |
Loadlock transfer arm | Rotary vane pump: down to 1x10-1 TorrPfeiffer turbomolecular pump: down to 1x10-7 Torr |
Gas control | Manual mass-flow-control (MFC) and manual ventOxygen, nitrogen and argon gases are available |
Computer | Windows XP, 32-bit operating system with Neocera PLD softwareLooping routine editor for automated growth of superlattice or intermixing between >2 materials |
Laser | Solid state and Quantronix laser: Nd:YAG laser
|
Optics | Mirrors (Purchased from Thorlabs Inc.)
Focus lens (Purchased from Thorlabs Inc.):
Detachable quartz window, Transmission ~94% |
Laser energy density | Optimal spot size: 1mm x 2.5mm rectangleAchievable energy density: ~10 J/cm2 Commonly-used energy density: 1-3 J/cm2 |
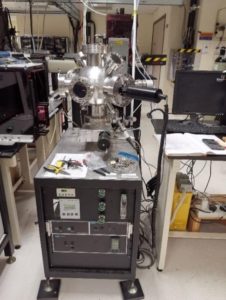
Pulsed Laser Deposition: Small Chamber
The Small Chamber is manufactured by Neocera. It is a convenient, automated pulsed laser deposition (PLD) system. It can be used for growth of various oxide, nitride and metal thin films.
Technical Specifications
Target holders: | 6 units of interchangeable carousels1 inch diameter stage Computerized raster (0-30o/s) and fix rotation Fixed target shutter |
Substrate holder: | 2 inch diameter wafer sizeManual substrate shutter |
Substrate heater &Temperature controller: | Resistive heating with computerized PID controllerMax. heater temperature 800 oC |
Vacuum: | Rotary vane pump: down to 1x10-2 TorrPfeiffer turbomolecular pump: down to 1x10-7 Torr |
Gas control: | Automated control of pressure, and manual vent of nitrogen is available |
Computer: | Windows XP, 32-bit operating system with Neocera PLD softwareLooping routine editor for automated growth of superlattice or intermixing between >2 materials |
Laser: | Coherent Compex KrF excimer laser:
|
Laser energy density: | Optimal spot size: 2mm x 2.5mm rectangleAchievable energy density: ~5 J/cm2 Commonly-used energy density: 1-3 J/cm2 |
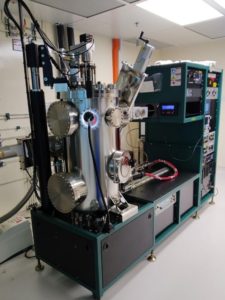
E-beam/Thermal Evaporator: AJA international-ATC-ORION-8E UHV
This UHV deposition system is capable of producing good quality thin films of metals, alloys and their multilayers Able to handle 8” wafers size. Targets E-beam: Ti, Cr, Al Thermal: Au, Cu
Technical Specifications
Load lock best vacuum: 10-7 torrMain chamber best vacuum: 10-9 torr
Cylindrical chamber size: 36″ high x 24″ diameter
Substrate rotation during deposition
Equipped with quartz thickness monitor
Four thermal evaporation sources (molybdenum boats) and 5 E-beam crucible sources (graphite)
Chemical Deposition
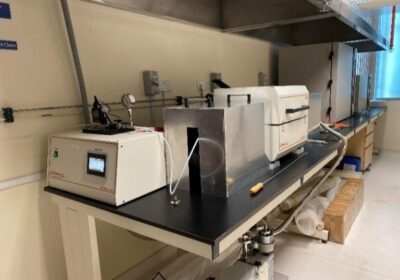
4″CVD
Technical Specifications
- 4” diameter split-tube single zone furnace
- Growth of Transition Metal Dichalcogenides
- Atmospheric pressure CVD
- Operating Temperature < 1000 C
- Gases: N2 (20-500 SCCM)
- Thermcraft | NanoOven Lab
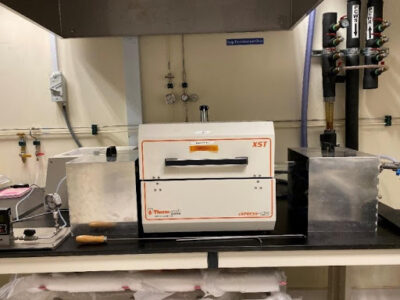
2″CVD
Technical Specifications
- 2” diameter split-tube single zone furnace
- Growth of Transition Metal Dichalcogenides
- Atmospheric pressure CVD
- Operating Temperature < 1000 C
- Gases: N2 (10-200 SCCM)
- Thermcraft | CVD Lab
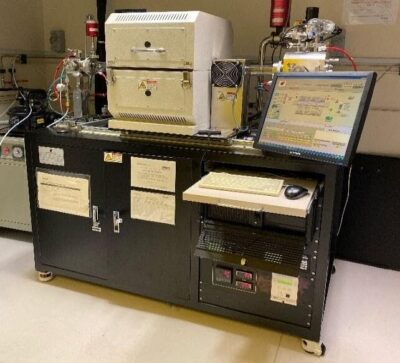
Graphene CVD
Technical Specifications
- Low Pressure CVD
- Standard Graphene growth on Cu
- Gases: CH4, H2, Ar
- Operating Temperature : 1050 C
- planarTECH | Furnace Lab
Chemical Synthesis
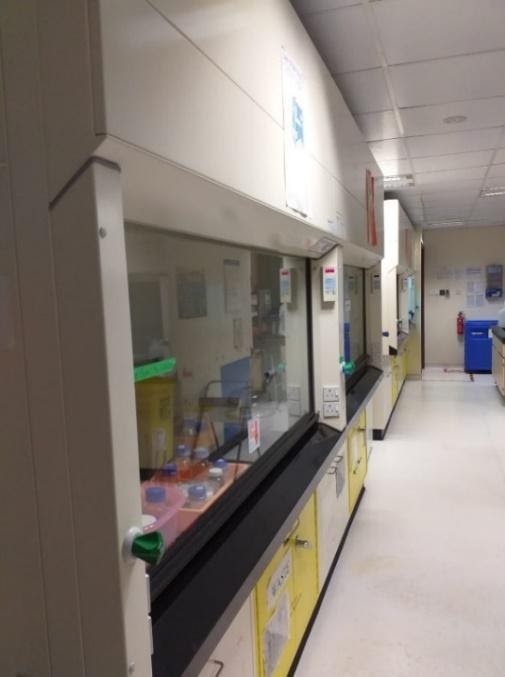
Flammable and acid fume hoods
Technical Specifications
The fume hood is often the primary control device for protecting laboratory workers when working with flammable and/or toxic chemicals. Nanoparticle Lab has equipped with one acid hoods and 10 flammable fume hoods for multipurpose usage.
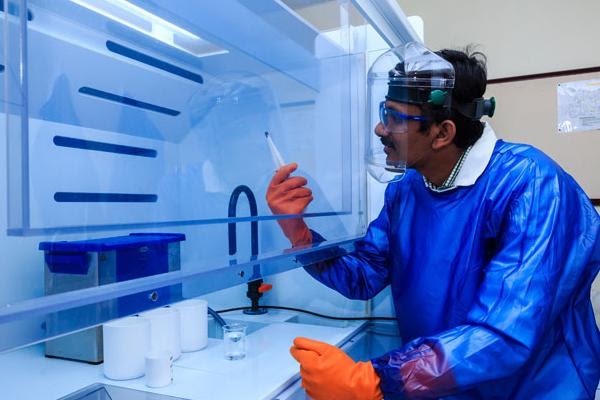
HF Workstation
Technical Specifications
- The HF (acid) workstation is suitable to process 5mm2 small substrates
- The process tank is incorporated with agitation mechanism such as DI water spray, N2 bubbling and 360 degree overflow function with effective rinsing of processed wafers
- Workstation body material: PP (white) Window material: Normal PVC (clear), 6mm Dimension: 1220 mm (L) X 1000 mm (D) X 1900 mm (H), Process Tank: Inner Dimension: 270 (L) X 270 mm (W) X 250 mm (H) for room temperature HF process, The workstation has built-in mechanical and electrical safety interlock to ensure the safety of the operator use
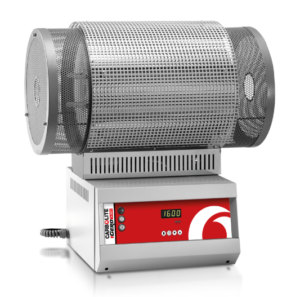
STF-16/180 Carbolite Tube Furnace
The HST-16/180 is mainly used for sintering PLD target pellets. Other usages include single crystal substrate annealing, control of oxygen vacancy migration and hydrogen doping in thin films.
Technical Specifications
Max. operating temperature | 1600 °C (current limit: 1300 °C) |
Number of heated zones | Single zone |
Furnace body | Horizontal configuration, work-tube insertion |
Control module | Carbolite Gero 301 PID controller, with single ramp to set-point and process timer |
Heating elements | Silicon carbide |
Work gas | Air, Ar, O2, N2, H2 (5%)/Ar (95%) |
Weight | 29 kg |
Dimensions:Max outer diameter accessory tube External furnace (excluding tube) |
60 mm625 mm (h) x 600 mm (l) x 375 mm (w) |
Heated length | 180 mm |
Recommended tube length | 600 mm (in air), 900 mm (in modified atmosphere) |
Uniform length ±5°C | 80 mm |
Max power | Max: 2500 W |
Thermocouple type | R |
Power supply required per phase | 200-240 V single phase 23 A |
Work tube materials | Quartz glass (<1050 oC), alumina (<1600 oC) |
Insulation plugs & radiation shields | Prevent heat loss & improve thermal uniformity |
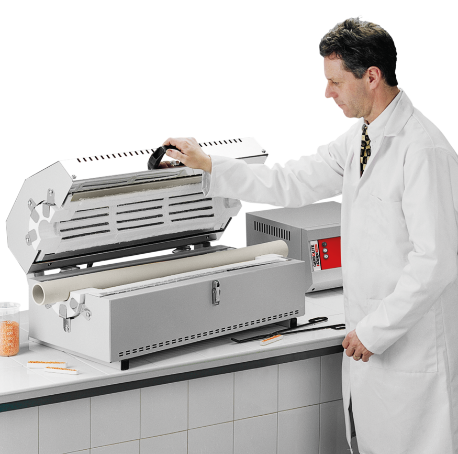
HST-12/600 Carbolite Split Tube Furnace
The HST-12/600 is mainly used for single crystal substrates annealing to allow surface reconstruction. Typically, substrates’ surface are desired to have unit-cell-high atomic terraces after the annealing to facilitate subsequent layer-by-layer thin film growth. Other usages include control of oxygen vacancy migration and hydrogen doping in thin films.
Technical Specifications
Max. operating temperature | 1200 °C (current limit: 1100 °C) |
Number of heated zones | Single zone |
Furnace body | Horizontal configuration, split into two halves to accommodate work tubes or samples fixed into a test rig |
Control module | Carbolite Gero 301 PID controller, with single ramp to set-point and process timer, separated from furnace by a 2-metre conduit |
Wire elements | High quality vacuum formed insulation, ensure fast heat up, excellent temperature uniformity and short cool down times |
Work gas | Air |
Weight | 38 kg |
Dimensions:Max outer diameter accessory tube External furnace (excluding tube Control module |
110 mm 350 mm (h) x 750 mm (l) x 410 mm (w)222 mm (h) x 376 mm (l) x 370 mm (w) |
Heated length | 600 mm |
Recommended tube length | 750 mm (in air) |
Uniform length ±5°C | 300 mm |
Max power | Max: 3000 W, holding: 1100 W |
Thermocouple type | N |
Work tube materials | Quartz glass (<1050 oC) |
Insulation plugs & radiation shields | Prevent heat loss & improve thermal uniformity |