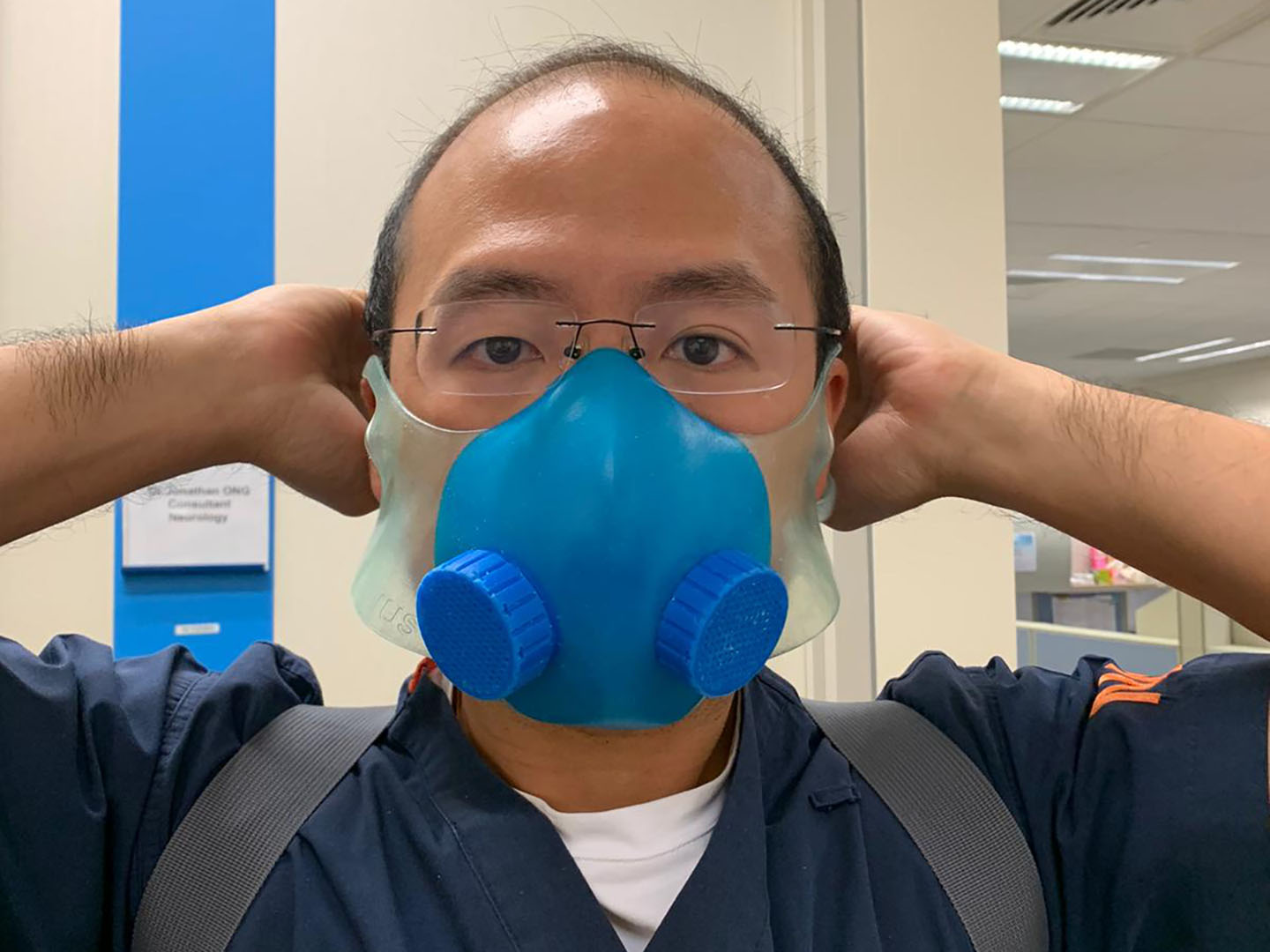
In the battle against COVID-19, one of the biggest challenges for healthcare workers is access to protective equipment that allows them to treat those infected with the virus whilst ensuring their own safety.
Masks are a particularly vital tool. But often the most secure masks are also the most cumbersome and uncomfortable to wear for extended periods, adding a further burden to already overstretched medics.
With this in mind, Professor Jerry Fuh from NUS Mechanical Engineering is leading a small team of researchers in NUS's Centre of Additive Manufacturing (AM.NUS) to rapidly prototype a new kind of comfortable and reusable soft mask using 3D printing technology.
We spoke to two of the researchers, project designer Michael Chung and doctoral student Guo Yilin, to get some insights into the project. Both are recent graduates from NUS Mechanical Engineering.
How did the project get started?
Michael:Â The initial idea for the masks came from physicians at NUH. They approached Prof Fuh with a concept for a better-fitting, highly secure mask that they could wear comfortably for extended periods. It also needs to be friendly for patients - using translucent materials - and for the environment, so it needs to be recyclable. As the designer, my job is to convert that initial concept quickly into something suitable for mass production.
Yilin:Â The concept is for a new kind of mask, made of soft silicone with easy to replace air filters. If this helps doctors and nurses to do their job more easily, comfortably and safely, they can treat more people more quickly. So it's a project where the impact will be really immediate.
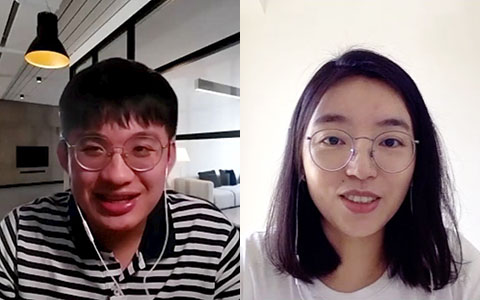
Why is 3D printing useful for this project?
Michael:Â 3D printing is great for turning concepts into reality much more cost-effectively and quickly than traditional development processes. It's a technology which has advanced really quickly in recent years and it still changing very rapidly. In the context of the pandemic, speed is obviously really important - so 3D printing means we can finalise the mask prototype quickly. Then we can get it into production and to where it is needed.
Yilin:Â The 3D printers we have at NUS are very advanced multi-material machines. This means we can test combinations of materials that affect the softness of the mask, so that we can find the best mix resulting in the most comfortable and effective mask for medics to wear.
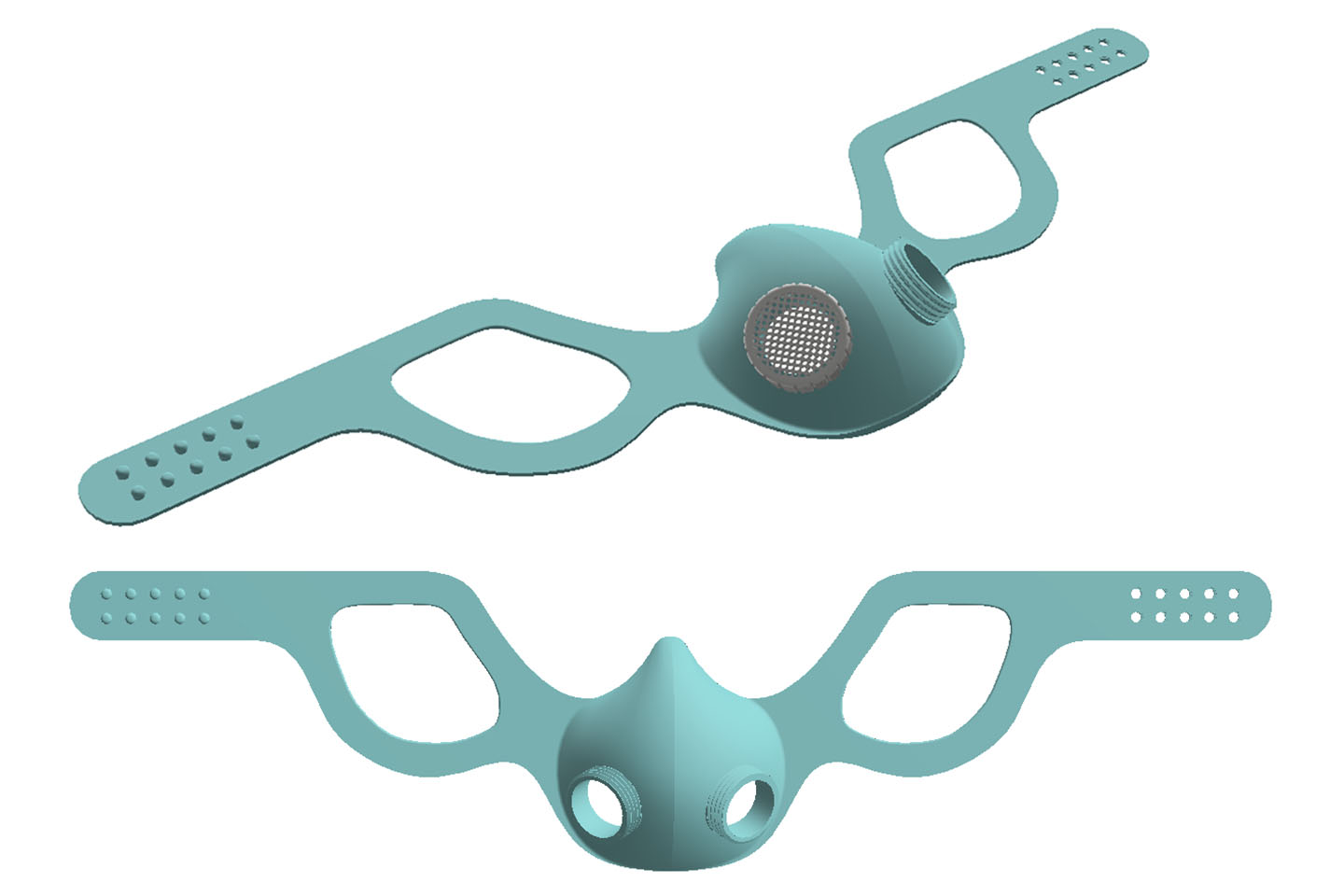
How have lockdown conditions affected how you do your work?
Yilin:Â Because of regulations, only people with special approval can access the lab where the 3D printers are. So most of the time I'm the only one there whilst most of our interactions and meetings as a team are over Zoom. It's a bit strange, but it's also quite efficient because we don't have to travel anywhere!
Michael:Â Because of lockdown rules, I'm not allowed to go into the lab but I can still access my lab computer from home. I use CAD (computer aided design) software called Fusion360 to work on the designs and refine the prototype based on feedback from the NUH medics and the team including Yilin.
How does it feel to be working on this project?
Yilin:Â Given the scale of the pandemic, there's pressure to work very quickly on this project. But being able to use the skills and technologies that we've been trained in to support frontline medical workers is really meaningful and motivating. When it goes into production and I see doctors wearing the mask I'll be very happy with that.
Michael:Â Â The medics we're working with have been very impressed with the prototypes they've tried and we've had a lot of positive and encouraging feedback. The main challenge is to develop a mask that closely fits a range of face shapes and sizes. But with the speed of 3D printing we can fine-tune the prototype quickly and get it tested with the people who will be using it. Hopefully, we'll get it into production soon. Helping medics here in Singapore and around the world will be very satisfying!