Transforming processes to slash carbon intensity
Follow CDE
PDF Download
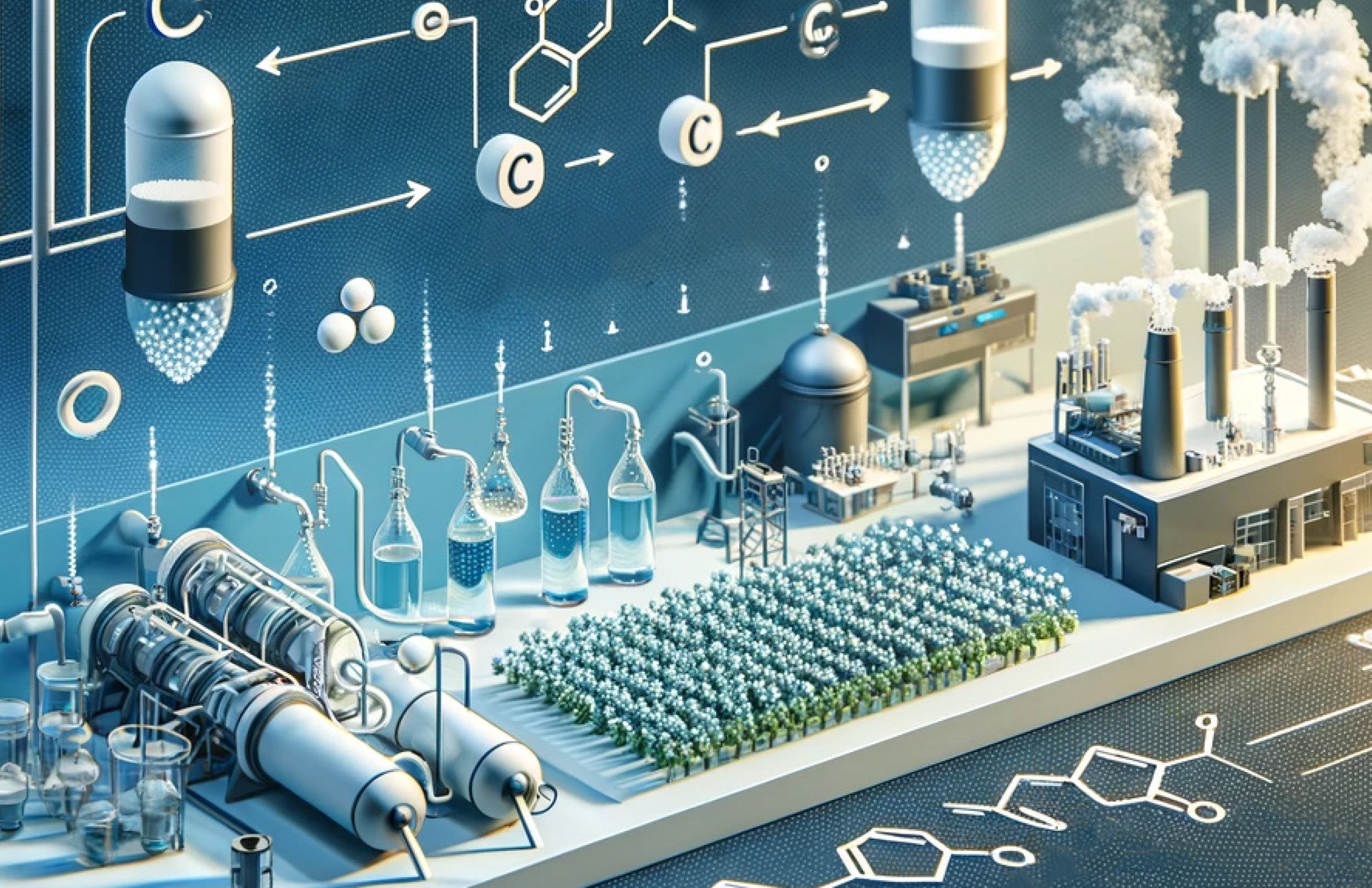
NUS CDE researchers design a novel and greener process to produce ethylene glycol, making use of carbon dioxide without emitting any wastes.
The transition to net-zero emissions is arguably one of the most pressing challenges of our time — not only prompting a rethink of how we produce, transport and consume but also driving transformations across virtually all major industries from the ground up.
Whether designing high-density batteries and advanced energy-storage solutions or promoting sustainable fuels in hard-to-abate sectors such as aviation, developing and deploying a diverse range of climate technologies is critical to reducing the amount of greenhouse gases we put into the atmosphere.
Researchers at the College of Design and Engineering, National University of Singapore, are delving into various climate mitigation strategies, with ongoing research efforts ranging from urban climate modelling to developing carbon-capture technologies.
At the Department of Chemical and Biomolecular Engineering, Assistant Professor Wang Lei is focusing on using carbon dioxide as the feedstock for producing important chemicals such as ethylene glycol, an essential building block in common items like household containers, clothing and antifreeze for cars and air-conditioning systems.
Advancing climate-positive chemical processes
Currently, producing the essential chemical is energy-intensive, leading to copious emissions of carbon dioxide and other wastes. With global production surpassing 40 megatons in 2020 — equivalent to almost 6 million elephants — the growing demand, expected to increase 5–10% annually, amplifies the need for more environmentally friendly production practices.
Addressing this challenge, Asst Prof Wang’s team developed a novel cascade catalytic system for the selective production of pure ethylene glycol. This process unfolds in two distinct steps — the first being an electrocatalytic reaction that generates a pure stream of hydrogen peroxide, followed by a thermal catalytic reaction where ethylene glycol is synthesised. The cascade system breaks away from traditional, highly polluting methods, combining the use of electricity and heat.
“The first electrochemical reactor constructed for this purpose showcased high Faradaic efficiency — exceeding 90% and allowed for adjustable current densities through a two-electron oxygen reduction reaction,” explains Asst Prof Wang. “This means the setup offers a low-energy alternative to conventional processes, all the while introducing modularity and the capacity to generate hydrogen peroxide on demand, obviating the need for storing and transporting the chemical.”
In the next thermal reactor, the generated hydrogen peroxide meets with ethylene, and with the help of a titanium-based catalyst and an acid, reacts to form ethylene glycol as the sole product — without any wastes. “Our design effectively decouples ethylene oxidation from electrode potentials, thus preventing the overoxidation of ethylene and streamlining both the reactor’s design and the downstream separation process,” adds Asst Prof Wang.
The team’s process achieved an efficiency of 70%—a significant improvement over existing methods — and demonstrated excellent stability, capable of continuous operation for up to 100 hours.
One step greener
“We also successfully adapted the process to produce ethylene glycol directly from carbon dioxide, bypassing the need for ethylene, which is derived from fossil fuels,” adds Asst Prof Wang. “This adaptation could complement nascent carbon-capture technologies, where the production of ethylene glycol could potentially turn into a climate-positive process.”
The applications of this cascade system are not confined to the production of ethylene glycol alone. Various other chemical reactions, such as methane and alcohol oxidation, and even epoxidation, which is a crucial step in formulating pharmaceuticals, can also benefit from the system.
“Our next steps involve optimising the system for enhanced efficiency and assessing its commercial potential. We’re also exploring how this technology can be applied to produce a wider range of chemicals,” adds Asst Prof Wang.
The team's findings were published in the journal Nature Catalysis on 26 June 2023.
Related
Wang Lei ▏Assistant Professor, Department of Chemical and Biomolecular Engineering
Related Departments
Read More
View Our Publications ▏Back to Forging New Frontiers - April 2024 Issue
If you are interested to connect with us, email us at cdenews@nus.edu.sg