Outdoor Mobile Robot for Tree Inspection
Project Motivation
One of the responsibilities of NParks is to conduct frequent inspections to check the health of about 6 million trees in Singapore. This is to prevent tree-care related accidents, which can affect humans, animals, vehicles and property. With the Singapore Green Plan 2030, there will be a rapid increase in the number of trees as well as a projected deterioration in weather patterns, which will lead to higher risk of tree falls. With a slow increase in the number of certified arborists in Singapore, it is predicted that the NParks’ arborists will be facing labour shortage and huge increase in workload by 2025.
To alleviate the labour shortage, a tree inspection robot was proposed to conduct repetitive and tedious tasks in the process of tree inspection. In general, the robot should be able to recognize and perform visual assessment of trees and at the same time, collect critical data that will be useful for the arborist. There can be one autonomous mobile robot at every park in Singapore to regularly inspect the trees in its vicinity. Therefore, this will reduce the workload burden on arborists and improve productivity in the tree inspection process as the arborists can focus on other demanding tasks that require human judgement.
Design
The proposed solution is an autonomous 6WD mobile robot with a rocker bogie suspension (similar to the Mars rover) that comprises various sensors for navigation and visual tree inspection. The purpose of the robot is to conduct the first level of inspection for the arborists and gather sufficient quality data that can be used to determine the health status of a tree.
Considering the worst terrains (30cm high obstacle, 30° slope) that the mobile platform has to overcome, the rocker bogie suspension was chosen. This suspension enables the robot to traverse on irregular terrains and climb large obstacles without compromising its stability. The wheels were made up of rubber tyres with directional thread patterns that can provide sufficient traction, especially in wet soil.
The rover has an array of sensors such as wheel encoders, inertial measurement unit (IMU), GPS, 3D LiDAR and depth camera to carry out the various tasks in navigation. The sensor data is fused together to accurately localise itself within the environment. Global path planners such as Dijkstra and A* is used to provide trajectories from one point to another. The rover then autonomously moves and avoids moving obstacles using algorithms like Dynamic Window Approach (DWA).
The rover’s camera utilises machine vision to “look” for defects along the tree trunk. It then measures the dimensions of detected defects. This information enables arborists to make a decision if further measures need to be taken.
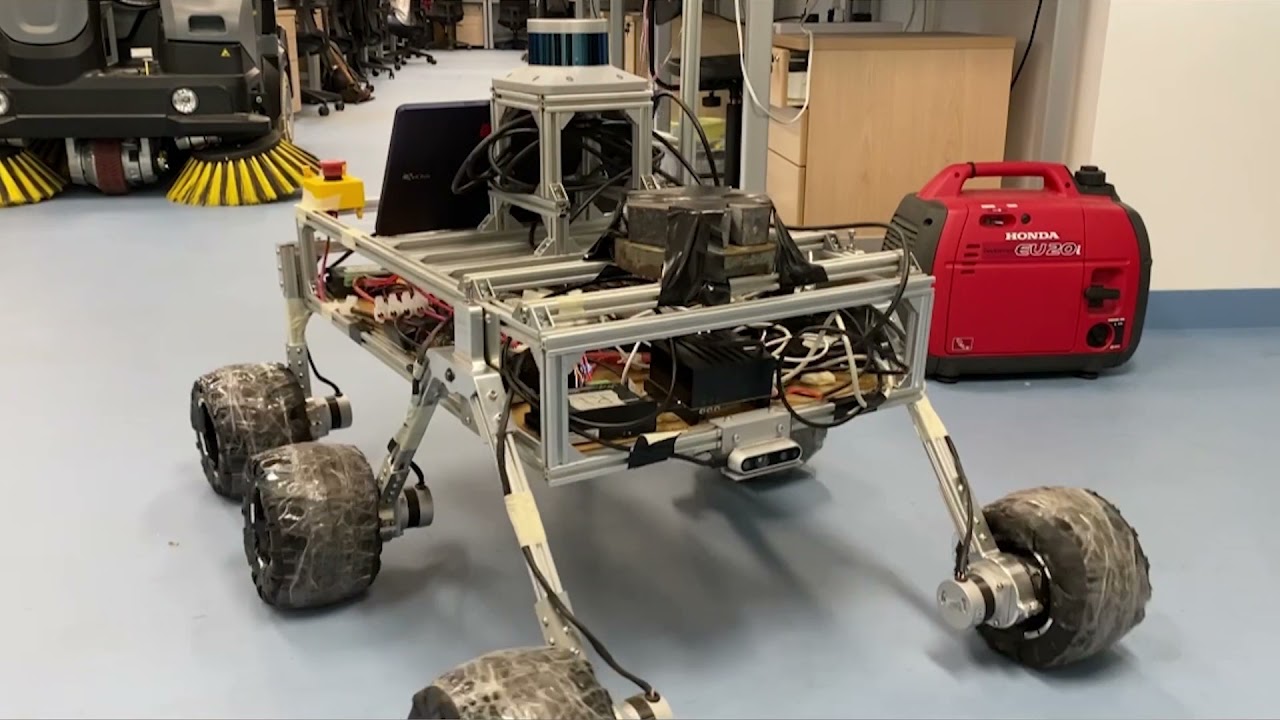
Project Team
Students:
- Arjun Agrawal (Mechanical Engineering, Class of 2021)
- Abdul Malek Bin Mohamed Yusoff (Mechanical Engineering, Class of 2021)
- Erwin B Zainul Shaffee (Mechanical Engineering, Class of 2021)
- Rafid Zuhayer Amin (Mechanical Engineering, Class of 2021)
Supervisors:
- Ang Marcelo H. Jr (mpeangh@nus.edu.sg)
- Ee Wei Han, Eugene (engewhe@nus.edu.sg)