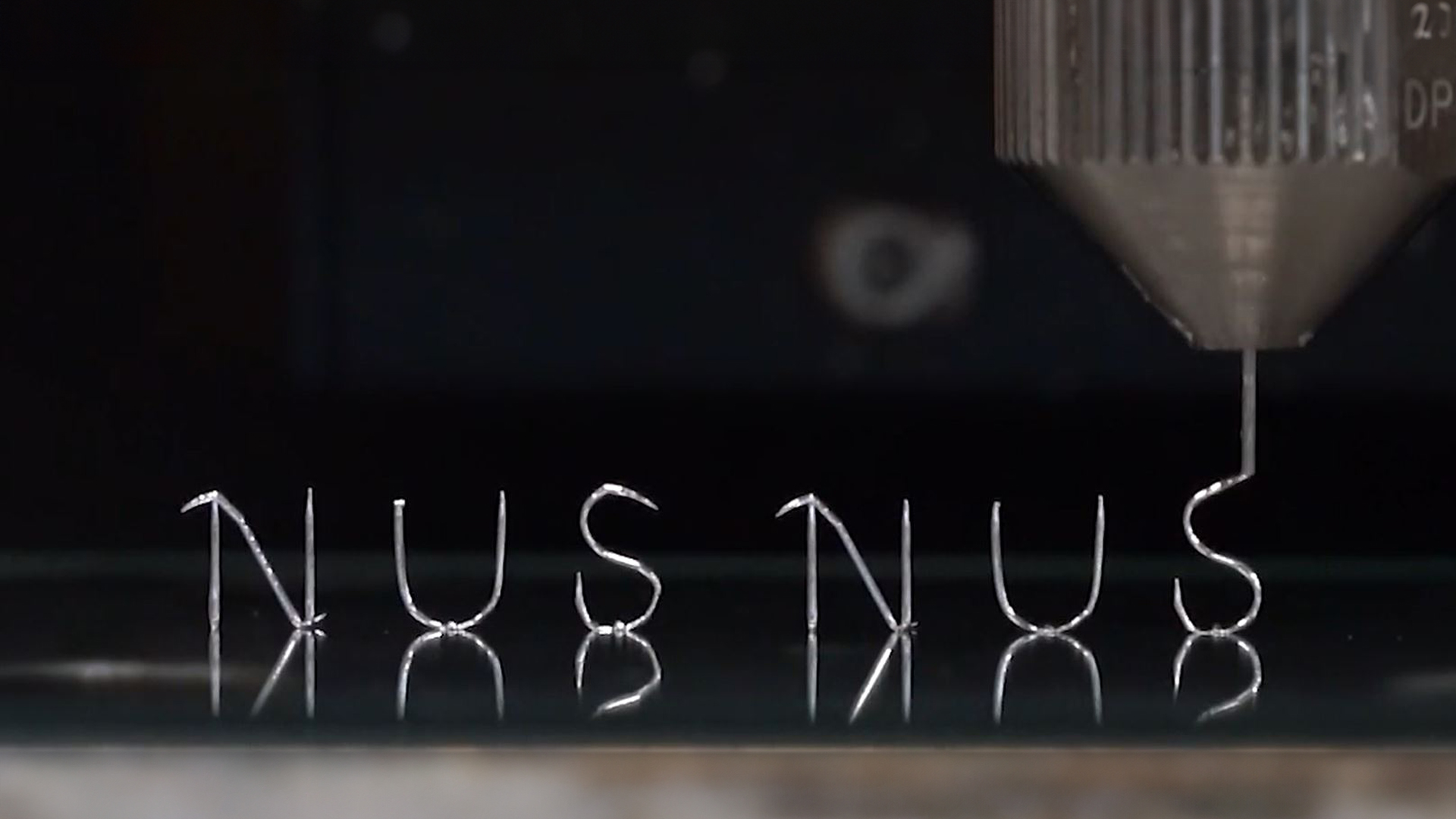
A novel 3D metal printing technique for fabricating advanced 3D electronic circuits could open the way to new generations of compact and powerful devices in applications such as healthcare, communications and security.
Named "CHARM3D" (conductive high-aspect-ratio metal 3D printing) the technique has been developed by a team led by Associate Professor Benjamin Tee (Materials Science and Engineering).
“CHARM3D offers high electrical conductivity, self-healing capabilities, and recyclability, making it a game-changer for electronics,” said Assoc Prof Tee. “Traditional circuit boards are flat, but 3D circuitry of the kind we can build quickly and at scale with CHARM3D allows components to be stacked and integrated vertically, saving space and enhancing device functionality.”
The CHARM3D technique leverages the unique properties of Field’s metal - a unique metal alloy with a low melting point of just 62 Celsius and which solidifies quickly. This allows for faster, more accurate printing without the need for additional support.
Existing 3D printing methods for circuits, like Direct Ink Writing (DIW), use composite inks that have low electrical conductivity and require support materials. However, in the CHARM3D technique, by using the natural tension between the molten Field’s metal in the printer's nozzle and the printed part, the researchers were able to produce uniform, smooth microwires directly on various surfaces, eliminating the need for external pressure and support materials.
Compared to conventional DIW, CHARM3D offers faster printing speeds of up to 100 millimetres per second and higher resolutions, enabling a greater level of detail and accuracy in circuit production.
“The CHARM3D technique allows us to rapidly create complex shapes such as vertical letters, cubic frameworks, and scalable helices without post-processing. These are not only uniform and smooth structures, but they are also highly conductive, self-healing, and recyclable,” said Dr Shaohua Ling, one of the lead co-authors of the research. He worked on the project when he was a Mechanical Engineering PhD candidate and conducted research in the laboratories of the Departments of Mechanical Engineering, Materials Science and Engineering, and Electrical and Computer Engineering.
The researchers’ findings were published recently in the journal Nature Electronics.
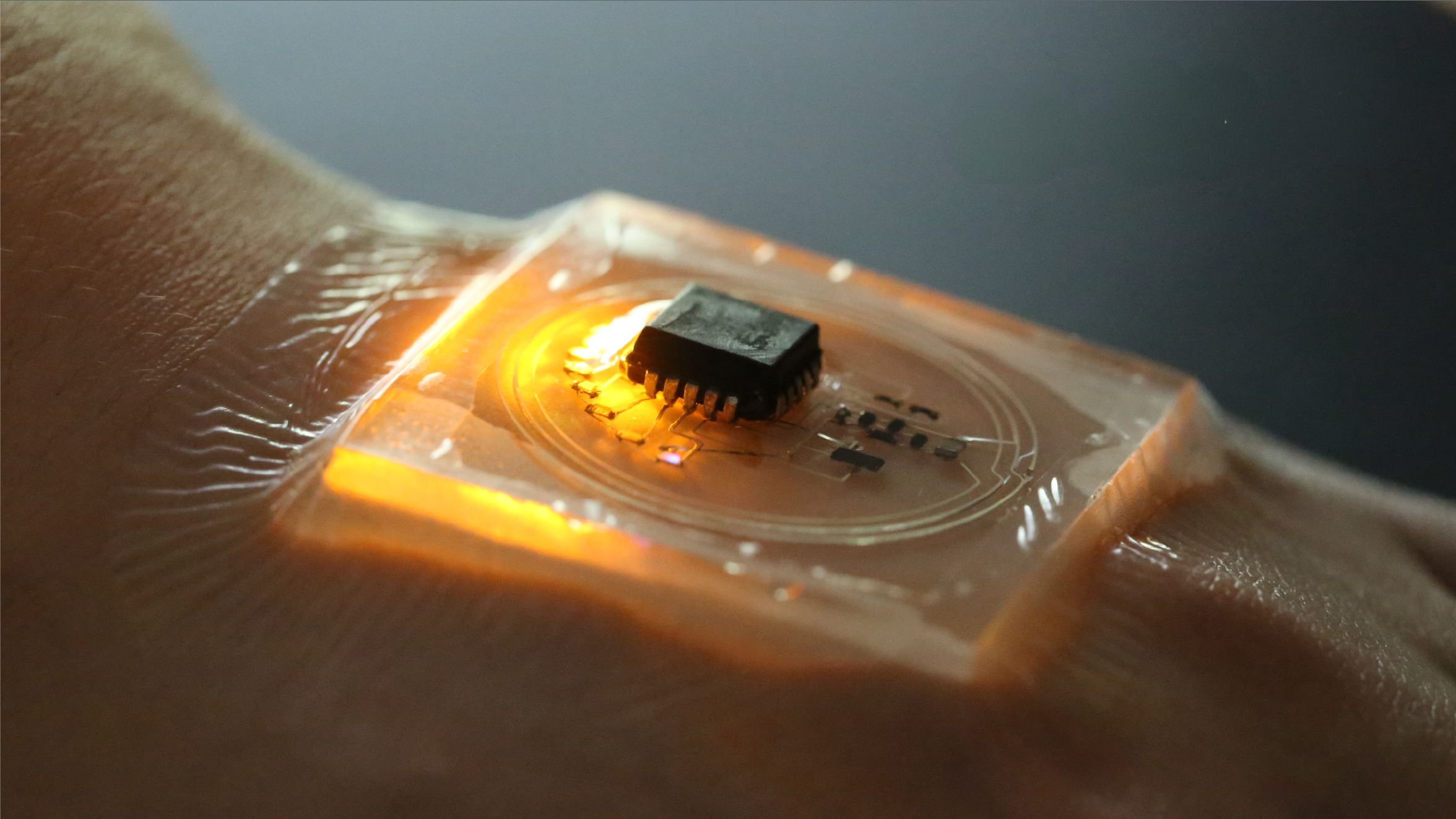
Practical applications
3D electronic circuits increasingly underpin modern electronics, from battery technology to robotics to sensors, enhancing their functionalities while enabling further miniaturisation.
“By offering a faster and simpler approach to 3D metal printing as a solution for advanced electronic circuit manufacturing, CHARM3D holds immense promise for the industrial-scale production and widespread adoption of intricate 3D electronic circuits,” said Assoc Prof Tee.
In healthcare situations, the researchers say CHARM3D technology could lead to the development of contactless vital sign monitoring devices, improving patient comfort and allowing continuous monitoring. In communication, it enhances the performance of 3D antennas, leading to better signal processing and more accurate medical imaging. The technique also has potential in security applications, improving detection systems.
The team successfully demonstrated CHARM3D by printing a variety of complex structures, including wearable battery-free temperature sensors and antennas for wireless monitoring. These developments could lead to significant improvements in medical devices, communication systems, and security technologies.
The researchers are now exploring ways to commercialise this technique and apply it to other metals and structural applications, potentially revolutionising the production of advanced electronic circuits.
Other collaborators in this work include Dr Zhuangjian Liu from Agency for Science, Technology and Research’s Institute of High Performance Computing and Professor Michael Dickey from North Carolina State University’s Department of Chemical and Biomolecular Engineering.