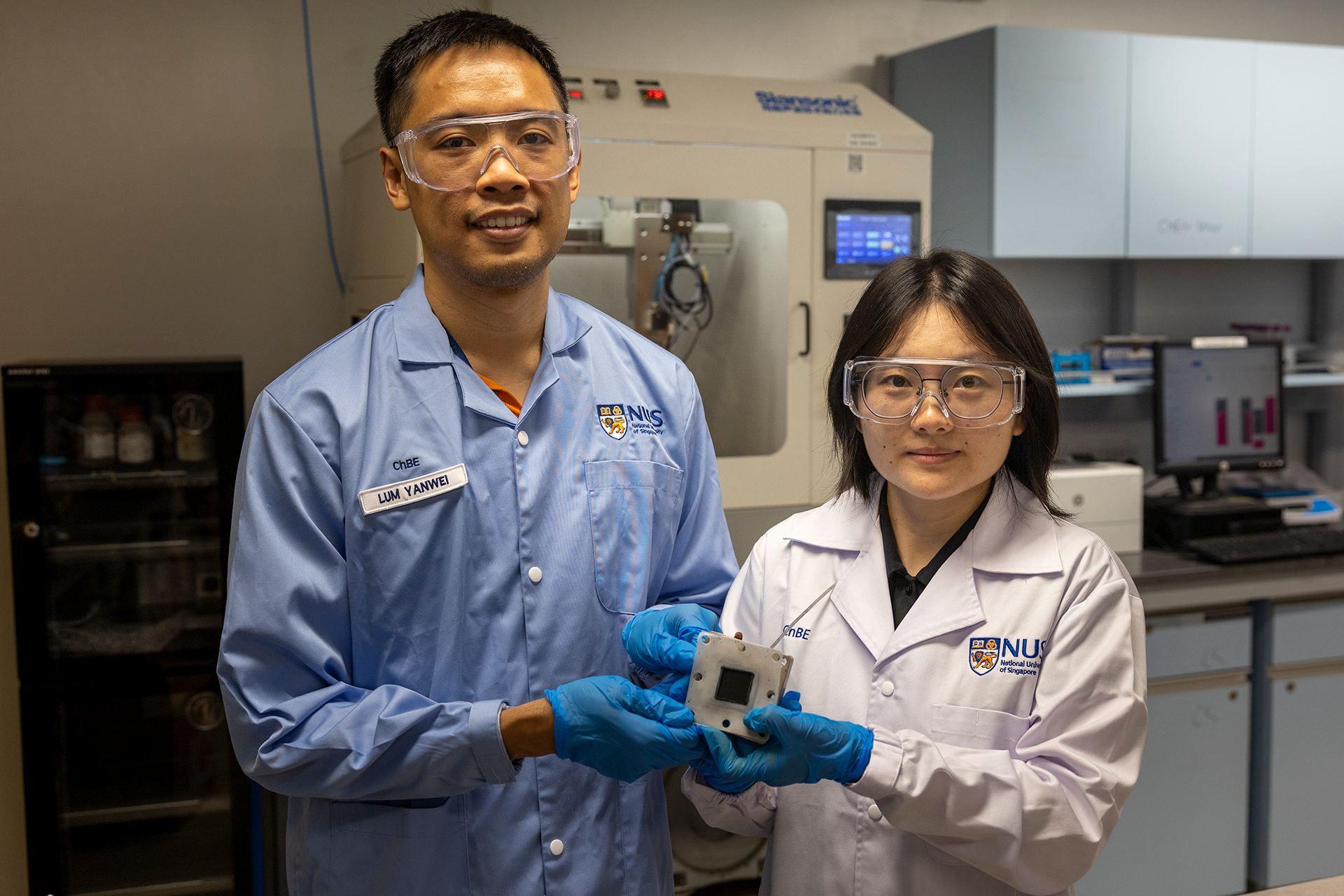
A new method to convert carbon dioxide (CO₂) into ethylene using significantly less energy than existing approaches could help cut emissions from one of the world’s most carbon-intensive manufacturing processes.
The catalyst at the heart of this breakthrough is the result of research led by Assistant Professor Lum Yanwei and Research Fellow Yang Qin, both from the Department of Chemical and Biomolecular Engineering and both affiliated with the NUS Centre for Hydrogen Innovations.
The team developed a copper-based material enhanced with small amounts of cobalt, known as dopants, which are added just below the surface of the catalyst. These dopants alter how the copper behaves during the reaction, enabling CO₂ to be converted into ethylene more efficiently and at a lower energy cost.
“By making precise changes at the atomic level, we were able to shift the most energy-demanding step in the reaction, which makes the overall process much more efficient,” said Asst Prof Lum. “This makes the process far more practical for industrial application.”
The team’s research was published on 25 July 2025 in the journal Nature Synthesis.
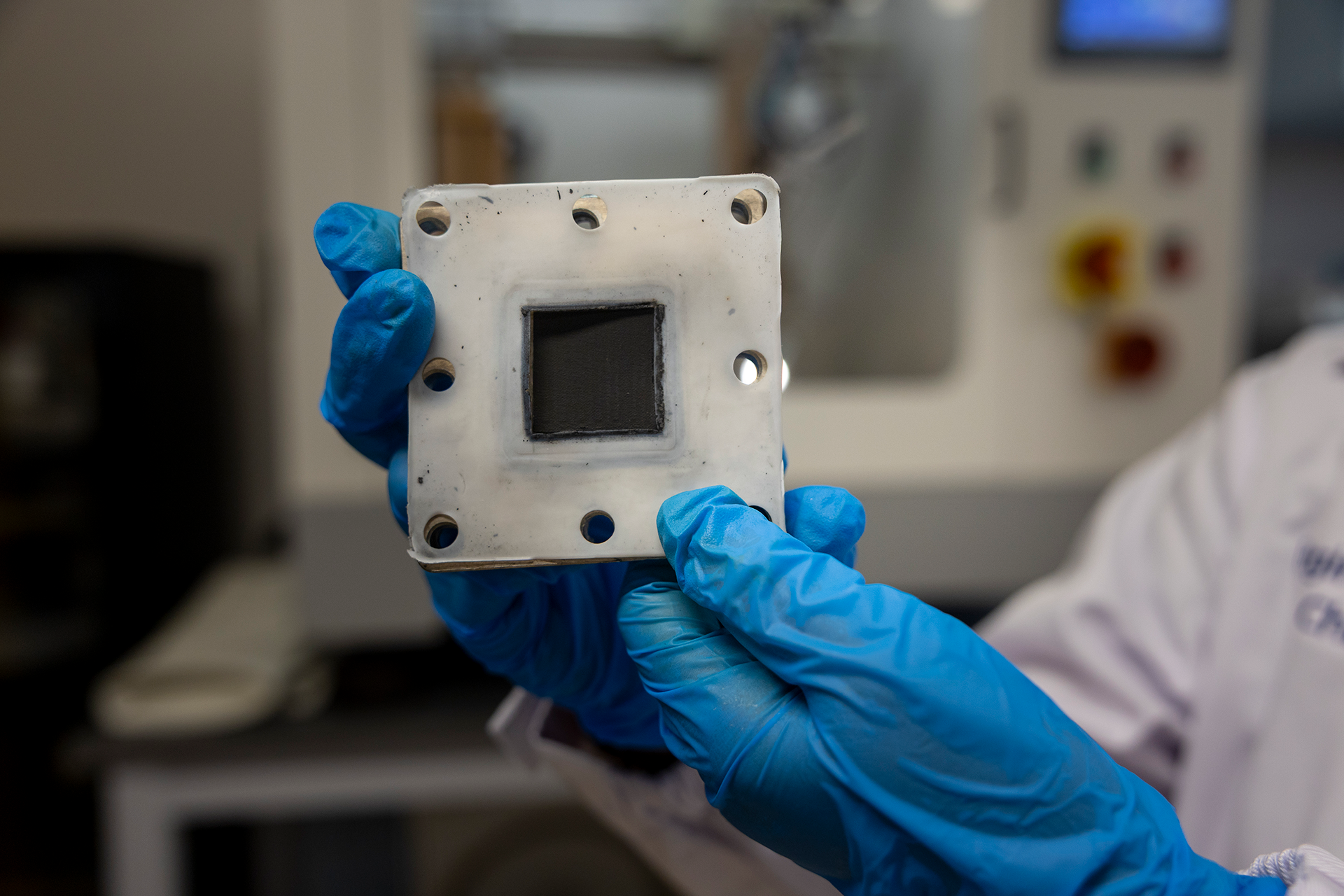
Ethylene is a key raw material used to make plastics, packaging, textiles and many other everyday products and is one of the most widely produced chemicals globally. However, most current ethylene manufacturing uses a process known as steam cracking, which involves heating fossil fuels to extremely high temperatures and releases large volumes of CO₂.
The new catalyst developed by Asst Prof Lum’s team was tested in a device known as a membrane electrode assembly, a compact, layered system that brings together the reactants, catalyst and electrical current in a tightly controlled environment. This design allows for efficient gas flow and product separation, and is commonly used in electrochemical technologies being developed for industrial use.
According to the researchers, the system delivered high ethylene output with more than 25 per cent energy efficiency and remained stable over 140 hours of continuous operation. “We also showed that the catalyst performed well producing ethylene from low-purity CO₂, such as that found in industrial flue gas,” said Asst Prof Lum. “This improves its potential for real-world deployment.”
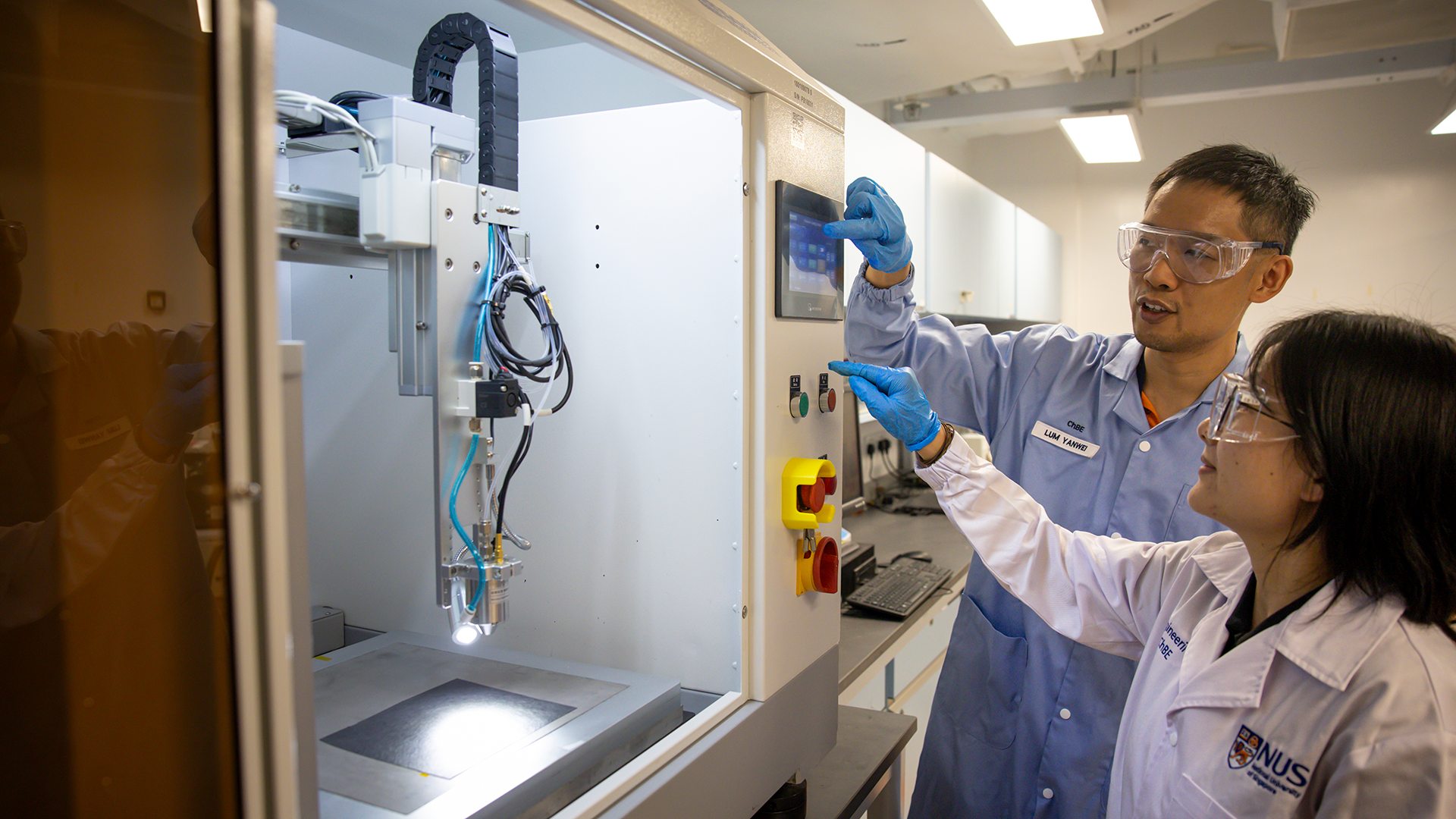
The discovery builds on earlier research led by Asst Prof Lum, which investigated how hydrogen atoms behave during CO₂ conversion. That fundamental work helped the researchers identify key bottlenecks in the reaction and informed the design of the new catalyst.
“Our previous work helped us pinpoint why the reaction tends to stall,” said Asst Prof Lum. “That gave us a clearer target for designing a better catalyst, and the results have exceeded expectations.”
A cost analysis by the research team suggests that, if powered by affordable renewable electricity, the process could produce ethylene at a cost comparable to conventional fossil fuel-based methods.
As global demand for ethylene continues to grow, the ability to manufacture it with lower carbon emissions could have a significant environmental benefit.
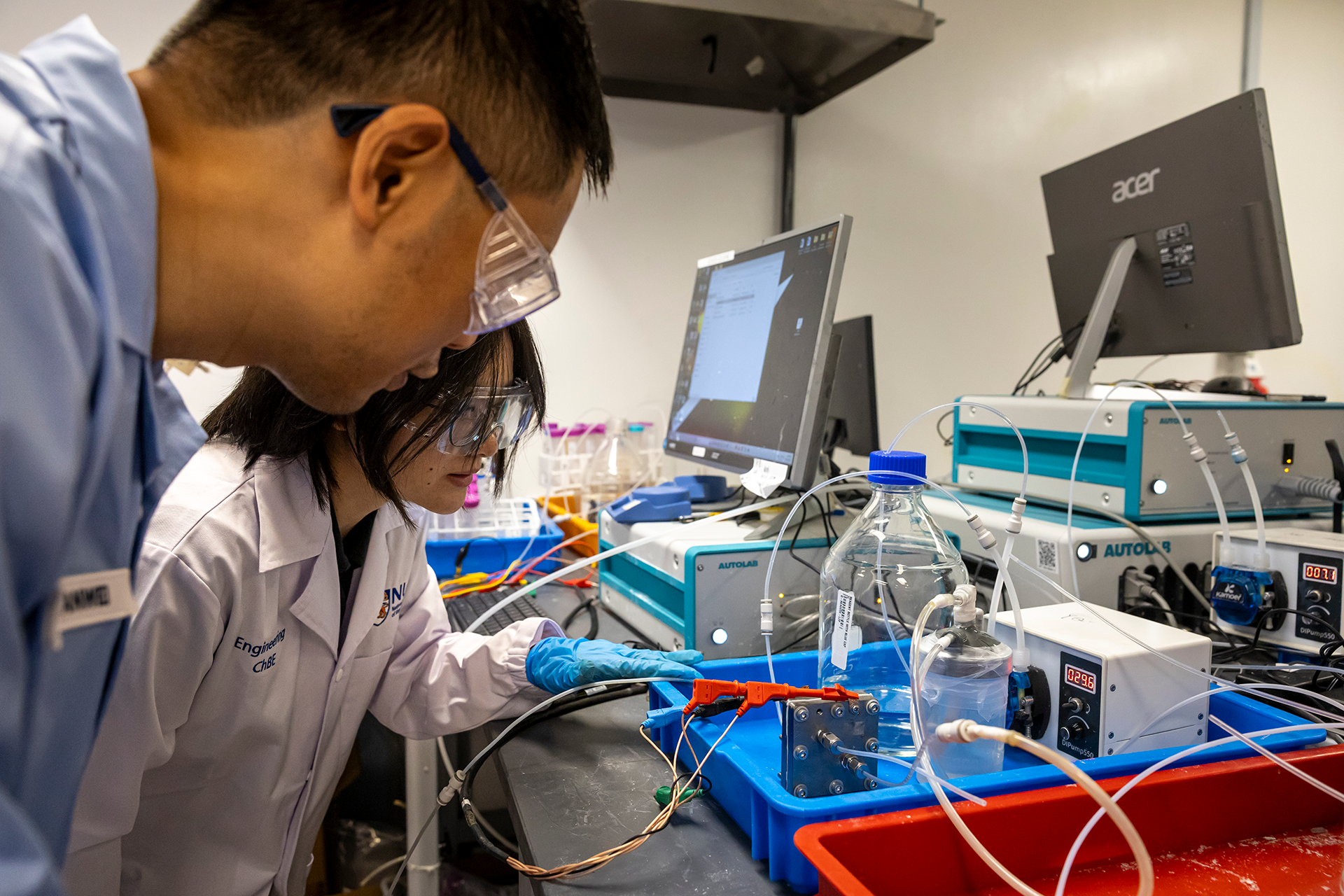