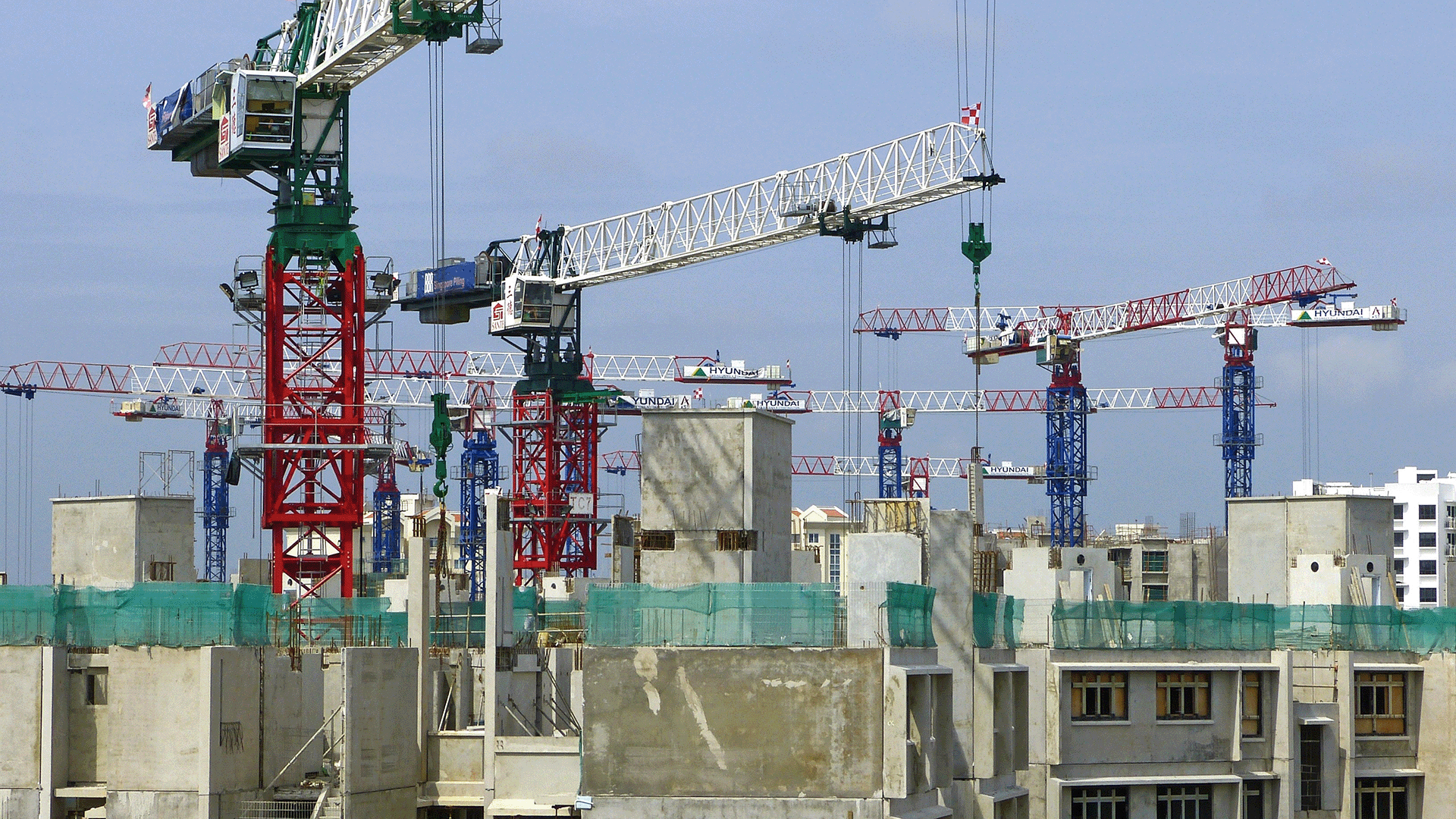
Like many industries, digital innovation is rapidly transforming the built environment sector. Dubbed by advocates as ‘Construction 4.0’, this technological transformation integrates advanced digital tools - such as building information modelling (BIM) systems and internet-connected sensors - to streamline operations and automate various aspects of the construction process, creating a more efficient and innovative sector.
But with the swift pace of change, coupled with the construction sector’s unique challenges and high operational costs, how can firms pinpoint which innovations are worth the investment and which to be more cautious with? After all, says Professor Florence Y. Y. Ling (Department of the Built Environment), not all new technologies are created equal; knowing where and when to invest can be a game-changer.
Prof Ling’s research interests include a strong focus on performance improvement of construction projects and increasing the competitiveness of construction enterprises. Her career began as one of a handful of women to thrive in the male-dominated construction industry, working as a cost engineer for eight years before she moved into academia and teaching.
Since then, she has published more than 170 international refereed journal papers and in one recent co-authored study published in the Journal of Construction Engineering and Management she explored which digital tools truly enhance the performance of architectural, engineering, and construction firms.
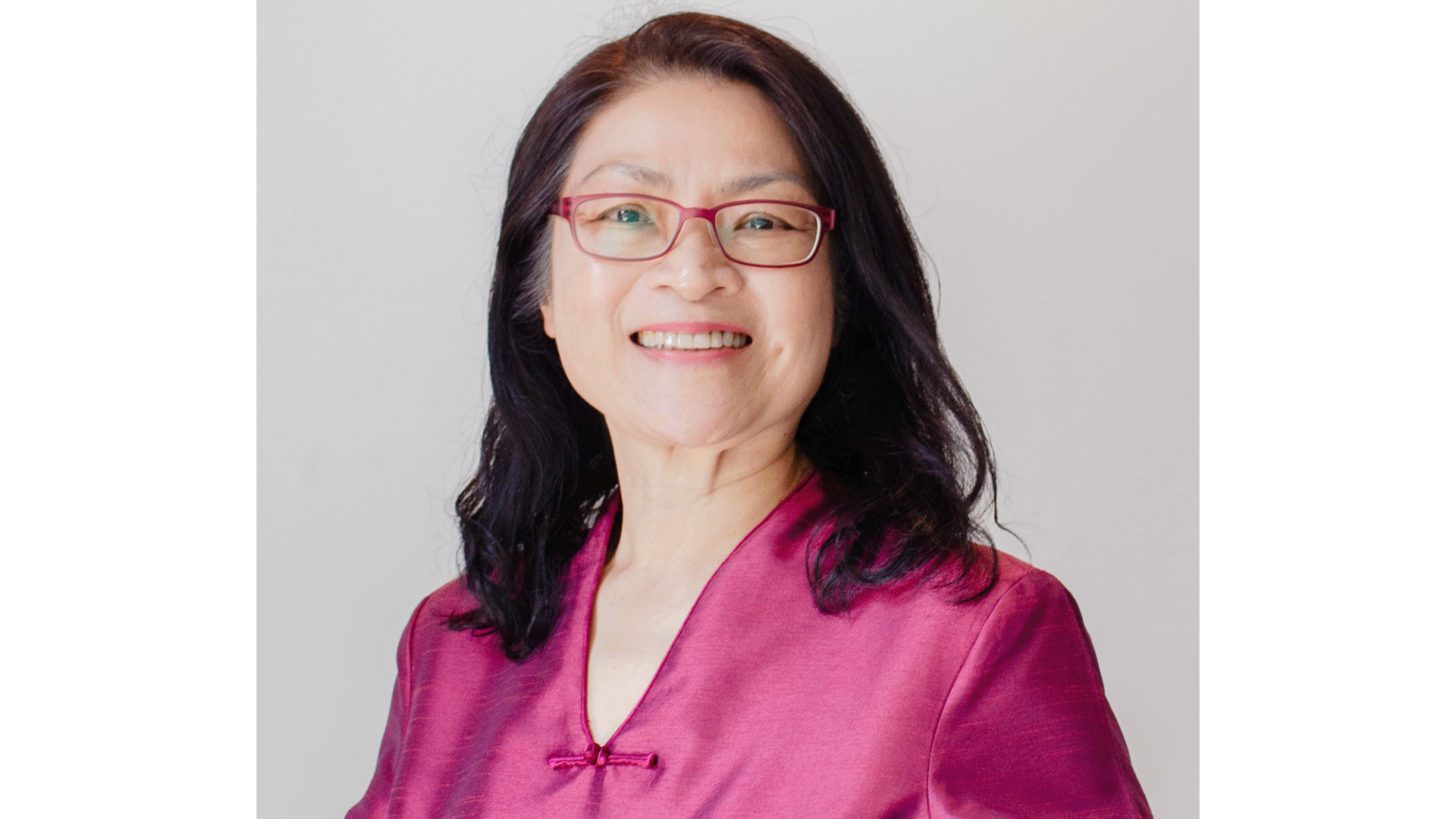
The study uses an in-depth online survey of 101 professionals from across Singapore’s built environment sector to highlight five ‘super technologies’ that the researchers say are creating significant impact. The data was gathered by Gerald Heng (Project and Facilities Management, Class of 2023) as part of his undergraduate Final Year Project, who is also named as a co-author on the paper and has since embarked on a career as a quantity surveyor.
“These digital technologies stand out for boosting a range of factors,” Prof Ling says, “from project quality and productivity, to tender success and professional market reputation.”
The ‘super technologies’ are:
- Cloud-Based Systems: These allow for real-time data access and collaboration, leading to better project management and communication.
- Design for Manufacturing and Assembly (DfMA): An approach that optimises the design process for ease of manufacture and assembly, improving efficiency and reducing waste.
- Internet of Things (IoT): IoT connects devices and systems, enabling seamless data collection and analysis, which enhances decision-making and operational efficiency.
- Robotics: Automation through robotics improves precision and safety in construction tasks, reducing labour costs and time.
- Artificial Intelligence (AI): AI enhances predictive analytics and project planning, allowing for smarter resource allocation and risk management.
Technologies to reconsider
Interestingly, as well as identifying the top performers, the study also found that some digital technologies, like blockchain and digital fabrication, do not currently offer the same advantage.
“In the case of blockchain, for example, despite the excitement around this technology, the data showed that while it may have potential further down the line, it offers very little currently for construction firms in the way of tangible return,” says Prof Ling.
“The reasons for this might be because it’s too complicated, there are too many subcontractors, or that costing in the industry is something regarded as a trade secret. Whatever the explanation, the essential point is that data-based insights like those taken from our study can allow firms to strategically prioritise their tech investments, ensuring maximum return without unnecessary expenditures.”
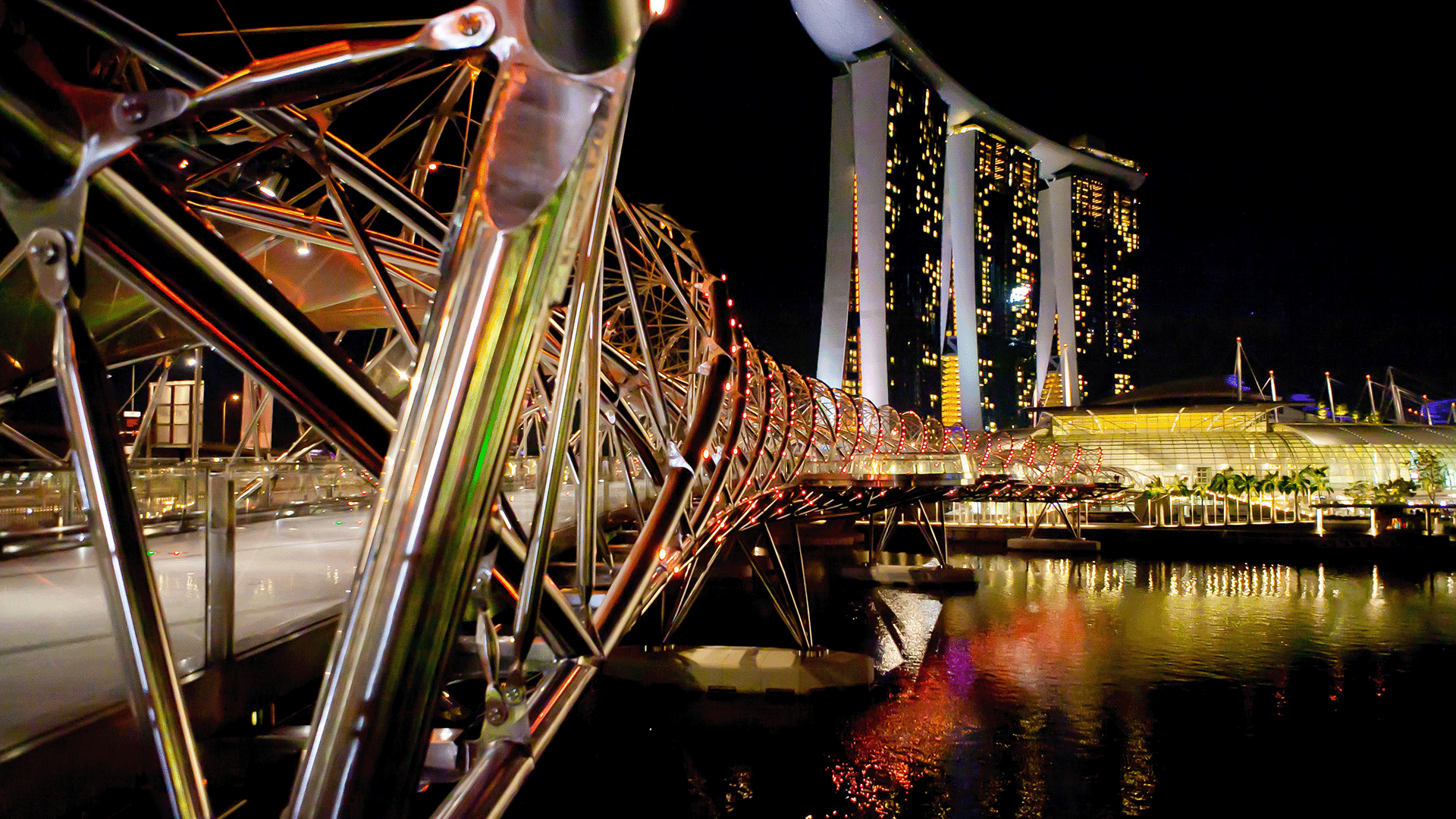
Technology adoption model
One outcome of the study is the creation of a technology adoption model, designed to guide firms on which specific technologies to implement. The model is based on a theoretical framework and statistical analysis, categorising technologies by their impact on four comparative advantage metrics: project quality, productivity, tender success, and reputation.
Using the model, each digital technology is placed into one of the model’s cells based on how many of the comparative advantage metrics it influences. At the top are technologies correlated with all four metrics - these should be adopted intensively. In the middle sections of the model are technologies correlated with three, two, and one metric, respectively, which Prof Ling says should be adopted steadily, cautiously, and after extensive evaluation. And finally at the bottom are technologies not significantly correlated with any metric, and hence adoption should be reconsidered or delayed.
“Our adoption model provides different levels of granularity, including overall findings applicable to the entire industry, as well as specific findings for contractors and consultants,” Prof Ling says, adding that the model can also be used as both a benchmarking tool and a decision-making aid.
Practical applications
Using the model for benchmarking, firms can compare their current digital technology use against the model to identify areas for improvement – for example, if a firm using cloud-based technology is not seeing higher project quality, productivity, and reputation, it should investigate the reasons behind this.
Likewise in decision-making, potential adopters can use the model to decide which technologies to invest in for maximum advantage - for example, contractors might prioritise AI, as it is associated with advantages across all four metrics.
Digitalisation is not only transforming efficiency and productivity but also plays a crucial role in achieving sustainability goals within the construction industry. Efforts to reduce carbon footprints are increasingly vital, and digital tools like AI and BIM are at the forefront of driving sustainability.
“Digitalisation and sustainability are two mega-trends that will shape the construction sector over the next few years,” says Prof Ling. “BIM, for example, can support precise planning and resource management, reducing waste and optimising energy use in buildings, whilst AI is a powerful tool for enhancing predictive analytics and resource allocation, further minimising environmental impact.”
She adds: “Embracing these technologies not only improves operational efficiency but also helps firms meet stringent environmental standards and reduce their carbon footprints.”
As firms in the built environment sector navigate the complexities of the digital age, Prof Ling says her study underscores the importance of informed technology adoption.
“Going forward, the role of digital technologies in Singapore’s construction sector is likely to escalate,” says Prof Ling, “especially with government initiatives aimed at improving productivity and cutting reliance on human labour. As such, it will be crucial for firms to adopt a strategic approach in integrating these digital tools to maximise their benefits.”