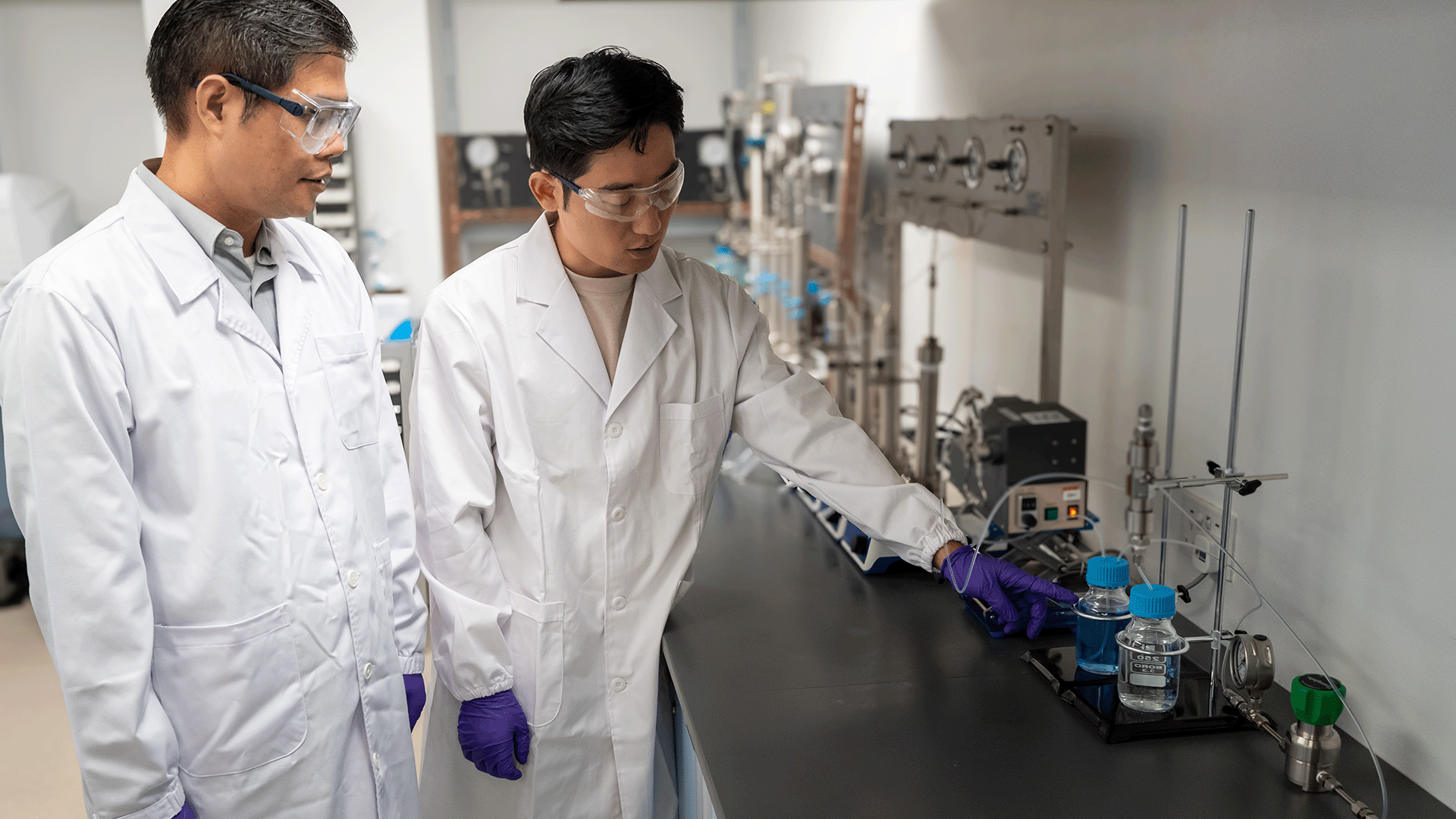
A new membrane technology using advanced metal-organic frameworks developed at CDE could be a significant step forward in cleaner and more sustainable chemical production. With its ability to separate very small and similar molecules in liquids, the researchers behind the membrane's development say it could have a particularly significant impact on industries like pharmaceuticals and energy.
Chemical manufacturing often requires the separation and purification of different molecules within liquids - a process that can be both challenging and energy-intensive. Moreover, methods currently used usually struggle with precision and durability, meaning they tend to wear out quickly, leading to a shorter lifespan, longer downtimes and other inefficiencies.
“Many of the existing methods are limited in their ability to separate complex mixtures with high precision and sustainability,” said Associate Professor Zhao Dan from the Department of Chemical and Biomolecular Engineering, who led the research behind the new technology. “Our new membrane technology addresses this by providing a solution that is both reliable and accurate, as well as being more efficient and environmentally friendly.”
The team’s research was published recently in the journal Nature Chemical Engineering.
The approach developed by Assoc Prof Zhao’s team involves a special kind of membrane made from a metal-organic framework (MOF) that can selectively filter out specific molecules. MOF materials were first developed in the 1990s, but have gained significant attention in recent years and seen substantial advancements due to their unique porous structures and potential applications.
MOFs are made from metal precursors linked by organic (carbon-based) materials, forming a structure with very small but very precise pores. MOF membranes can be thought of as tiny, customisable filters at the molecular level. The pores in MOF membranes are uniform and strong, allowing the membrane to effectively and consistently separate different molecules in liquids.
What distinguishes this new technology developed by Assoc Prof Zhao’s team is its creation process. The researchers used a method involving two different metals to produce a unique structure in the MOF. This structure, enhanced by the bimetallic approach, provides more accessible pores to upgrade filtration efficiency while enabling high molecular selectivity and durability, allowing the membrane to operate continuously for over 1,500 hours without significant performance degradation. This makes it much more reliable for industrial use.
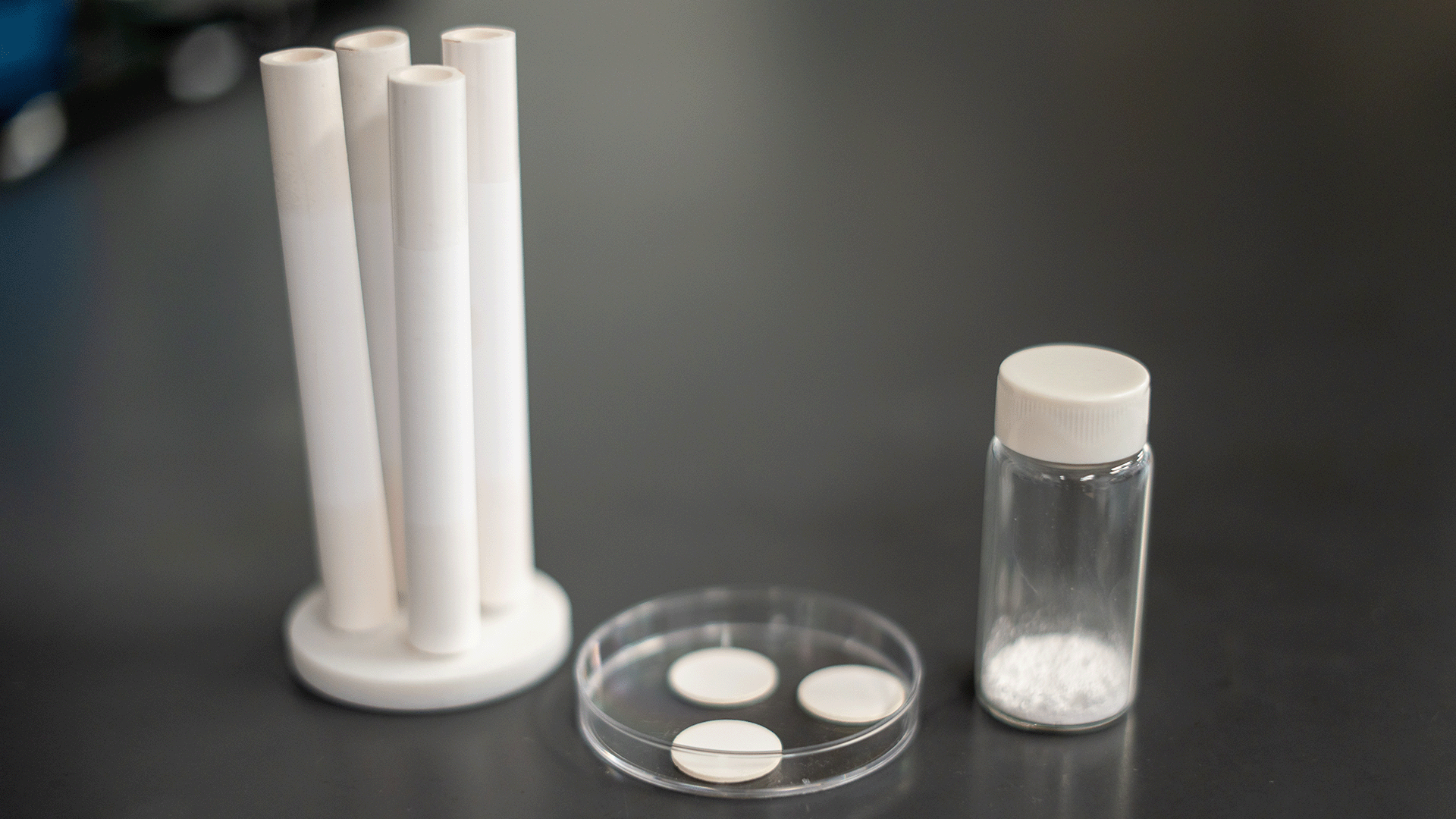
“Taking a bimetallic approach has allowed us to create a membrane that is not only highly efficient but also long-lasting,” said Associate Professor Zhao. “This is crucial for industrial applications where downtime and maintenance can be costly.”
This new membrane could be transformative for industries that rely on chemical separations, such as pharmaceutical companies that produce medicines. It can help purify and recover valuable chemicals more efficiently, saving time, energy, and money. The membrane’s ability to separate complex mixtures of small molecules with high precision ensures that the desired products are obtained more effectively.
“This technology has the potential to simplify and improve many industrial processes,” said Assoc Prof Zhao. “By making separations more precise, we can enhance the quality of the final products and reduce waste.”
One of the biggest challenges with older membrane technologies is their tendency to wear out quickly and their lack of accuracy. The new MOF membrane, however, is both durable and highly accurate. The team also established a correlation between the membrane’s pore size and its ability to reject unwanted molecules, which will assist in predicting how the membrane will perform and could guide future improvements.
“The durability and precision of our membrane are the two major factors that set it apart from existing membrane technologies,” said Associate Prof Zhao. “Our work going into this research has also given us a much better understanding of how these MOF membranes work and their potential capabilities, which will guide future designs and improvements.”
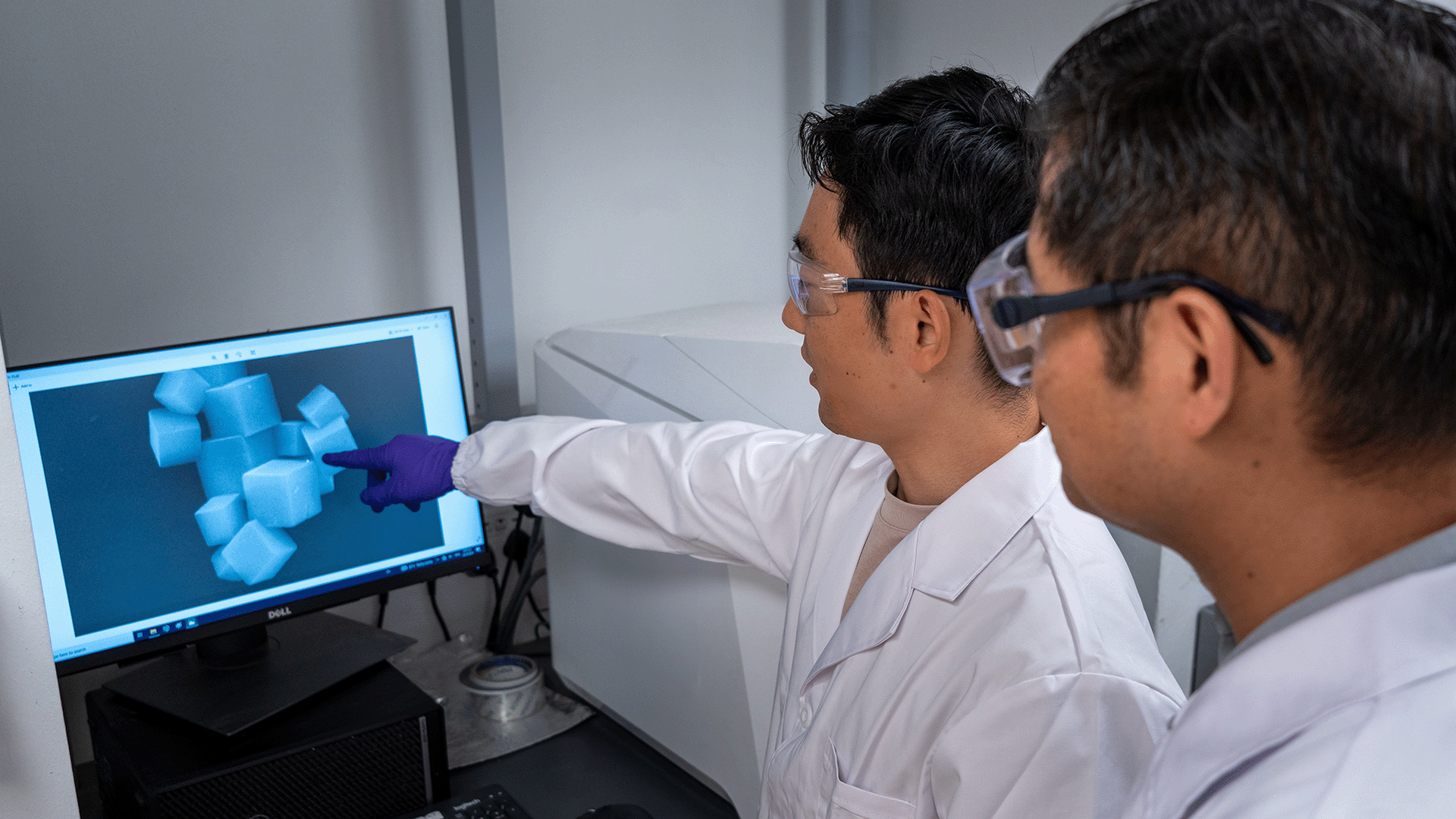
Compared to existing filters, the greater efficiency of the new MOF membrane means it can process liquids at a faster rate, significantly reducing the time and energy needed for chemical production. For example, when filtering methanol (a common industrial solvent), the new membrane performs up to 50 times better than standard membranes.
“This membrane’s efficiency is remarkable,” said Assoc Prof Zhao. “By using less energy and lasting longer, it represents a more sustainable approach to chemical manufacturing.”
The research team says the potential benefits of this technology as it develops further are extensive. In the pharmaceutical industry, for example, the membrane can help purify drugs more efficiently and mildly without damaging sensitive ingredients. It can also assist in recycling solvents, making the production process more sustainable. The membrane has already proven effective in separating and purifying various compounds used in medicines, such as curcumin and vitamin B12.
“Our goal is to make chemical processes cleaner and more efficient,” said Assoc Prof Zhao. “This membrane technology is a practical step in that direction.”
With that in mind, Assoc Prof Zhao and his team have begun working with industry partners, including pharmaceutical giant Pfizer, to refine and scale up the technology and take it from the lab to the factory floor and eventually widespread industrial use.
“Collaborations are key to realising the full potential of this technology,” Assoc Prof Zhao said. “With further development, we look forward to seeing it make a real difference, helping industries reduce their environmental impact and shaping the future of sustainable chemical manufacturing.”
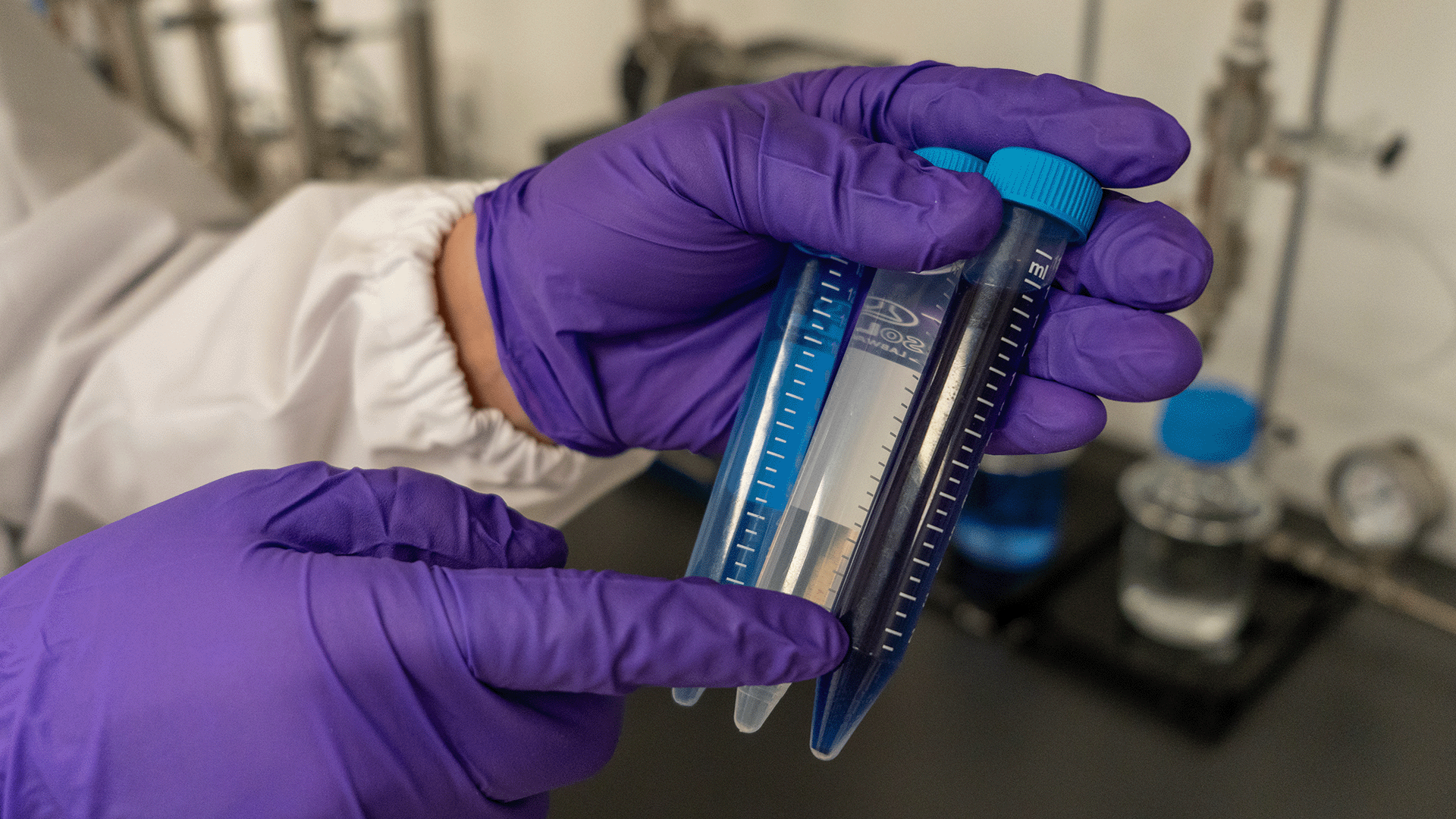