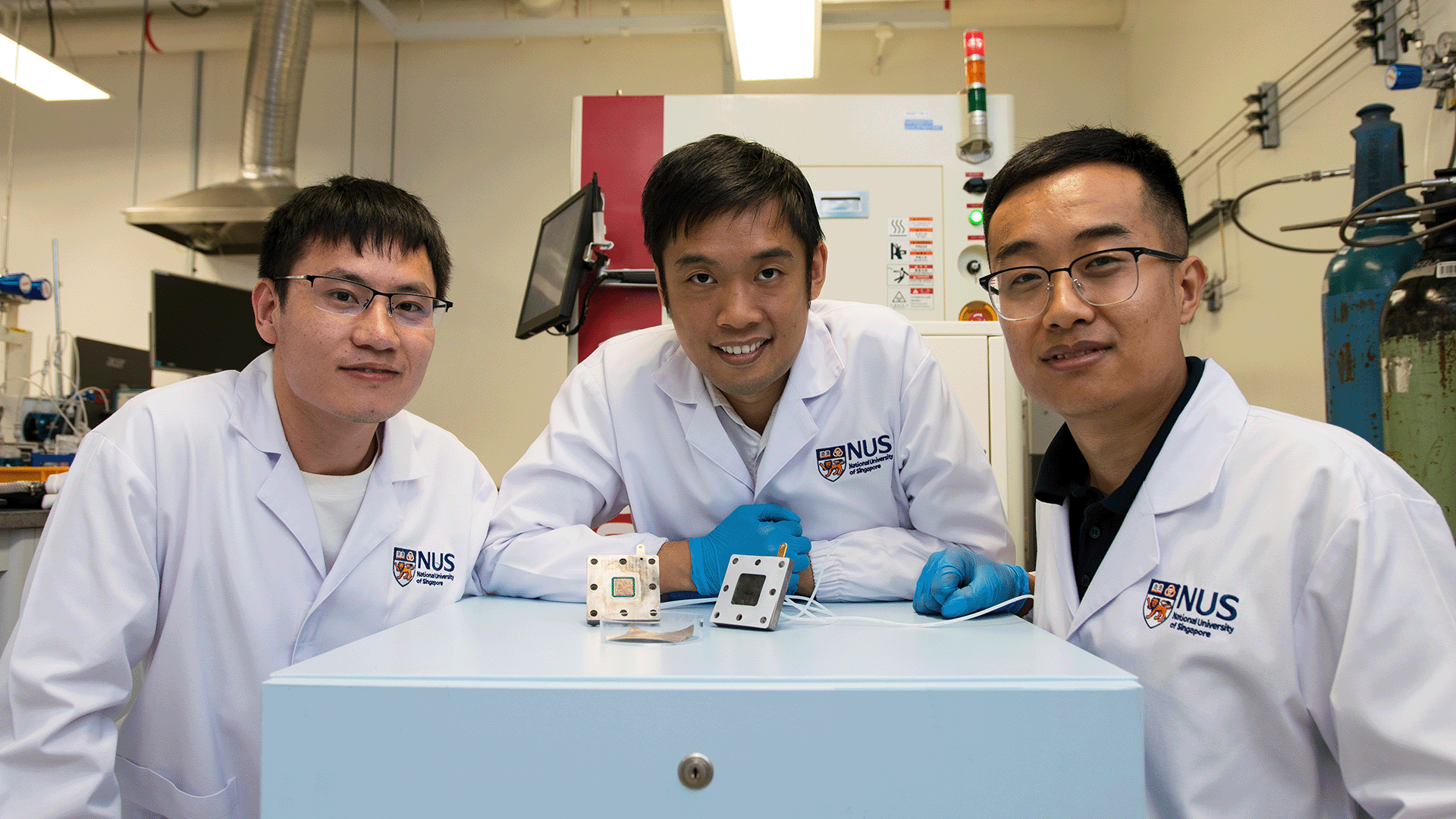
A new energy-efficient, cost-effective technique of converting waste carbon dioxide into value-added chemicals and fuels could help to cut emissions and slow the impact of climate change.
The technique, developed by a team of researchers at CDE led by Assistant Professor Lum Yanwei (Chemical and Biomolecular Engineering), enables the direct conversion of CO2 from treated flue gas, a common by-product of industrial processes, into high-value multi-carbon (C2+) products such as ethylene and ethanol. These are essential raw materials for the production of various everyday compounds such as plastics, polymers and detergents. Furthermore, unlike other conversion methods, the new technique does not require high-purity CO2.
Electrochemical reduction of CO2 has been seen as a promising method for transforming waste CO2 into a range of valuable feedstocks for chemicals and fuels. However, most established methods have required high-purity CO2, significantly increasing costs due to the energy-intensive purification process from sources like flue gases. Additionally, the presence of oxygen impurities in flue gas results in undesired side reactions, significantly reducing the efficiency of the CO2 reduction process.
Asst Prof Lum’s team at CDE aimed to sidestep these challenges by integrating catalyst design with electrolyte selection. In their study, which was published earlier this year in Nature Communications, the researchers first introduced a new method to design catalysts with greatly enhanced efficiencies for the electrochemical conversion of CO2. Utilising this approach, they designed a nickel catalyst boasting exceptional performance for CO2 reduction, achieving an efficiency rate exceeding 99 percent.
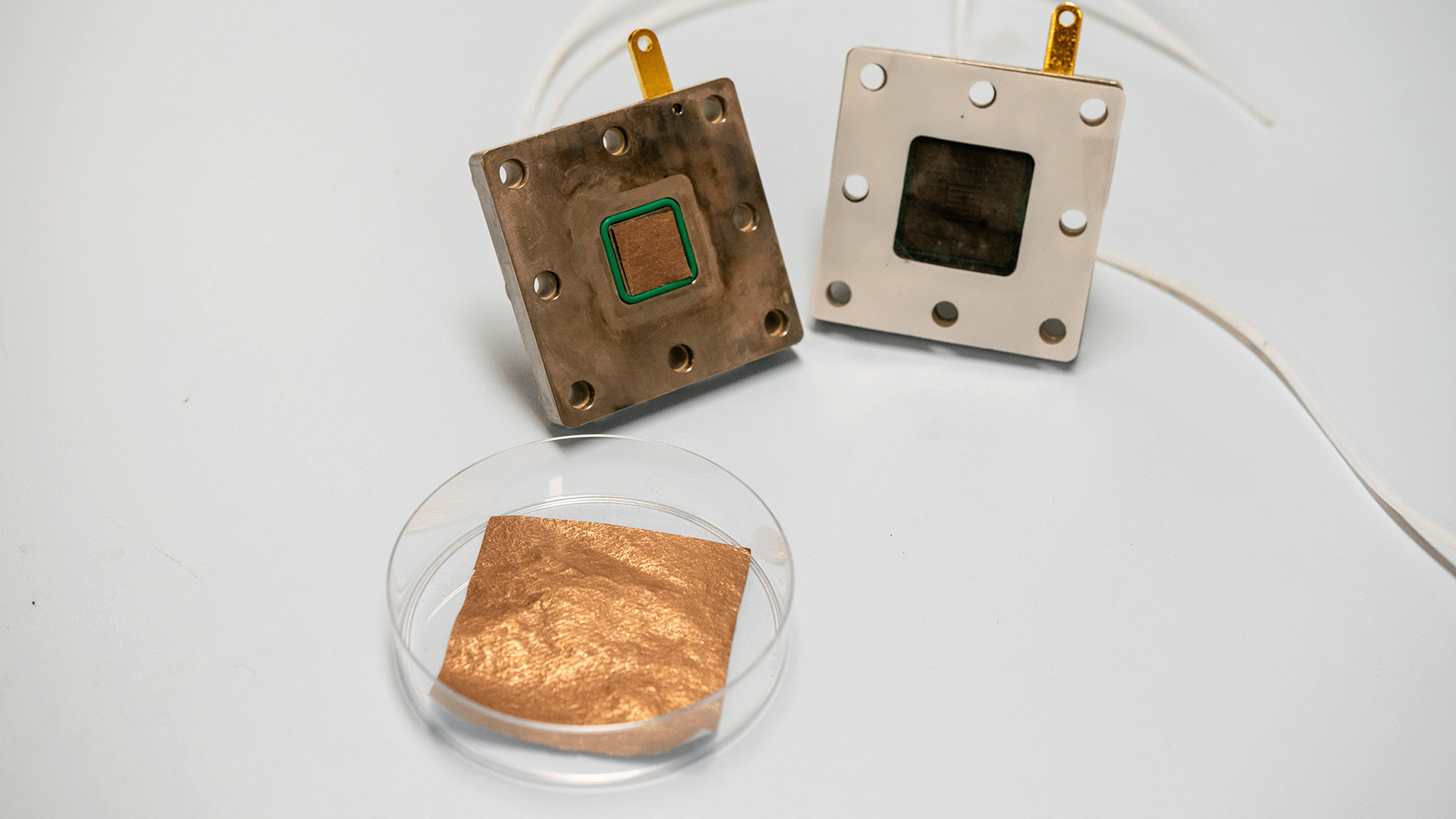
Building on this study, in a separate paper also published in Nature Communications, the team designed a composite system by sequentially layering this nickel catalyst onto a copper surface. By integrating acidic electrolytes with this composite system they found they were able to significantly suppress the side reactions from oxygen impurities in flue gas, achieving a performance comparable with systems that utilise pure CO2 as feedstock.
Highlighting the potential savings of using their new technique, Asst Prof Lum said: “The cost of purifying CO2 can amount to about USD 70 to 100 per ton, which can constitute about 30 per cent of the costs involved in converting CO2 to feedstocks such as ethylene through electrochemical means. Our novel technique demonstrates a potential pathway for the development of efficient electrolysers for the direct conversion of CO2 in flue gas, using simple yet effective electrolyte and catalyst design strategies to advance integrated sustainability solutions.”
The potential applications of this research extend beyond the production of ethylene and ethanol. By adjusting the catalyst system, the team says their technique could be applied to synthesise other valuable chemicals, such as acetate and propanol which are used in the production of everyday products such as adhesives and disinfectants.
“We are seeing strong interest from the industry and are currently in talks with some companies to further advance this research,” said Asst Prof Lum. “Our goal is to enhance the energy efficiency and scalability of our system, moving beyond laboratory-scale experiments towards developing prototype reactors that can be applied in industrial settings.”